MENU
CH | CHF
-
-
-
-
- Forum Labo 2025
- Advanced Therapies Week (ATW) 2025
- SLAS Europe 2025
- Bioprocessing Summit Europe 2025
- Medlab Middle East 2025
- SLAS International 2025
- Biologics World Nordics 2025
- ASIA LABEX: The Lab Show 2025
- BioProcess International Europe 2025
- ISEV 2025
- Future Labs Live 2025
- DataHow Symposium 2025
- Cell 2025
- LabDays 2025
- ILMAC 2025
- ASIA LABEX: The Lab Show 2025
-
-
-
-
- Forum Labo 2025
- Advanced Therapies Week (ATW) 2025
- SLAS Europe 2025
- Bioprocessing Summit Europe 2025
- Medlab Middle East 2025
- SLAS International 2025
- Biologics World Nordics 2025
- ASIA LABEX: The Lab Show 2025
- BioProcess International Europe 2025
- ISEV 2025
- Future Labs Live 2025
- DataHow Symposium 2025
- Cell 2025
- LabDays 2025
- ILMAC 2025
- ASIA LABEX: The Lab Show 2025
CH | CHF
-
- Benchtop Centrifuges
- Floor-Standing Centrifuges
- Refrigerated Centrifuges
- Microcentrifuges
- Multipurpose Centrifuges
- High-Speed Centrifuges
- Ultracentrifuges
- Concentrator
- IVD Products
- High-Speed and Ultracentrifuge Consumables
- Centrifuge Tubes
- Centrifuge Plates
- Device Management Software
- Sample and Information Management
-
- All Pipettes, Dispensers & Automated Liquid Handlers
- Mechanical Pipettes
- Electronic Pipettes
- Multi-Channel Pipettes
- Positive Displacement Pipettes & Dispensers
- Automated Pipetting
- Bottle-Top Dispensers
- Pipette Controllers
- Pipette Tips
- Automation Consumables
- Dispenser & Pipette Accessories
- Automation Accessories
- Dispenser & Pipette Services
Sorry, we couldn't find anything on our website containing your search term.
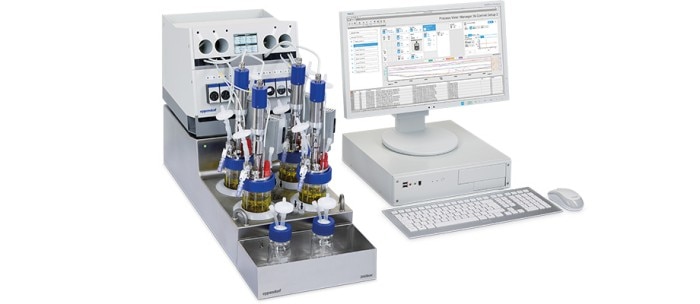
Constant RQ Fermentation of Pichia pastoris in the DASbox® Mini Bioreactor System
NINA SCHRAND, MALTE SCHNEIDER, EPPENDORF SE BIOPROCESS CENTER, JUELICH, GERMANY MA SHA, BIOPROCESS APPLICATIONS LAB, EPPENDORF, INC., ENFIELD, CT, USA
The yeast Pichia pastoris is largely used for heterologous protein production in biotechnology. For optimizing the production yield, one of the most important factors is the feeding strategy. One of the leading strategies for protein production-oriented feeding is based on the respiratory quotient (RQ). Constant RQ-based feeding ensures that the respiratory metabolism of glucose/glycerol is optimized for protein production purposes and the formation of by-products is limited [1].
The intention of this study is to demonstrate the feasibility of constant RQ-based feeding for protein production-oriented yeast fermentation using the DASbox Mini Bioreactor System . Further, we compared the results to a standard DO-spike triggered feeding done in the same setup.
The respiratory quotient (RQ)
RQ is the quotient of carbon dioxide produced and oxygen consumed by a culture, expressed with the carbon dioxide transfer rate (CTR) and the oxygen uptake rate (OUR). Under conditions of a constant dissolved oxygen concentration, the OUR equals the oxygen transfer rate (OTR) [2]. The RQ for the metabolization of glucose is 1. This can be explained by the fact that per mol glucose, 6 mol O2 are needed and 6 mol CO2 are produced. Which means that the O2 uptake equals the CO2 transmission and thus their quotient is 1. Once glucose is fully metabolized the culture starts to consume fermentation by-products, mainly ethanol. As ethanol is more reduced than glucose, the use of ethanol as substrate results in a RQ value below 1.
Thus, the RQ value can serve as an inline parameter indicating which substrate is consumed by the culture, and a constant RQ process can be used to optimize fermentation based on a specific carbon source.
Materials and methods
In this study we used the Pichia pastoris strain DSMZ 70382. We used the DASbox Mini Bioreactor System (Eppendorf) for microbial fermentation applications. We connected a DASGIP® GA4 exhaust gas analyzer module (Eppendorf) and used DASware® control software (Eppendorf).
Medium preparation, setup of the bioprocess system, inoculum preparation, and optical density measurements are described in the Eppendorf Application Note 439 [3]. The process parameters are listed in Table 1.
The intention of this study is to demonstrate the feasibility of constant RQ-based feeding for protein production-oriented yeast fermentation using the DASbox Mini Bioreactor System . Further, we compared the results to a standard DO-spike triggered feeding done in the same setup.
The respiratory quotient (RQ)
RQ is the quotient of carbon dioxide produced and oxygen consumed by a culture, expressed with the carbon dioxide transfer rate (CTR) and the oxygen uptake rate (OUR). Under conditions of a constant dissolved oxygen concentration, the OUR equals the oxygen transfer rate (OTR) [2]. The RQ for the metabolization of glucose is 1. This can be explained by the fact that per mol glucose, 6 mol O2 are needed and 6 mol CO2 are produced. Which means that the O2 uptake equals the CO2 transmission and thus their quotient is 1. Once glucose is fully metabolized the culture starts to consume fermentation by-products, mainly ethanol. As ethanol is more reduced than glucose, the use of ethanol as substrate results in a RQ value below 1.
Thus, the RQ value can serve as an inline parameter indicating which substrate is consumed by the culture, and a constant RQ process can be used to optimize fermentation based on a specific carbon source.
Materials and methods
In this study we used the Pichia pastoris strain DSMZ 70382. We used the DASbox Mini Bioreactor System (Eppendorf) for microbial fermentation applications. We connected a DASGIP® GA4 exhaust gas analyzer module (Eppendorf) and used DASware® control software (Eppendorf).
Medium preparation, setup of the bioprocess system, inoculum preparation, and optical density measurements are described in the Eppendorf Application Note 439 [3]. The process parameters are listed in Table 1.
Read more
Read less
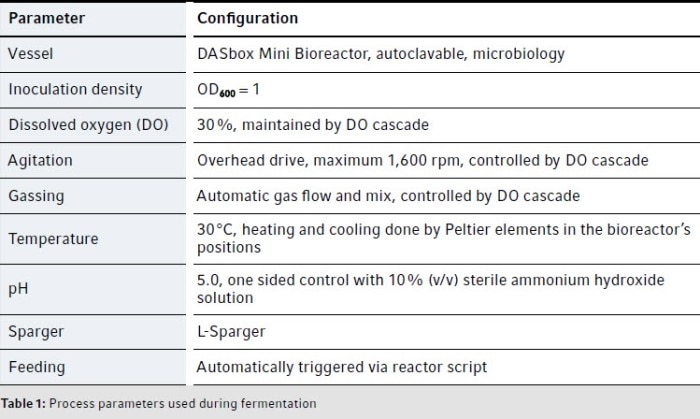
Feed process triggered by DO-spike
The end of the batch phase of a fed-batch culture is often indicated by a DO-spike. At this point, the carbon source within the initial culture medium is consumed, the metabolic activity of the culture and, therefore, its oxygen demand drop rapidly, resulting in a sharp increase of DO in the medium. We took advantage of this DO-spike to trigger an automatic start of the feed pump using an automatic programming script. The details are described in the Eppendorf Application Note 439 [3].
Automatic RQ control by programmed feeding
As stated before, the RQ value can serve as an indicator for which substrate is used by the culture. We implemented a software script which starts automatically after inoculation [3]. After a delay time of 12 h, the RQ value of 1 is used to start the feeding pump, and further feeding is automatically controlled based on the RQ value.
Results
We ran P. pastoris fed-batch fermentation two times. In one setup, the feed was started automatically by a script which was triggered by a DO-spike. In the other setup, we implemented a constant RQ-controlled feeding strategy.
The DO-spike based feeding was started once the value of dissolved oxygen raised from 30 % to above 38 % which was the case after 39 h inoculation time [3]. The RQ-controlled feeding was started after a delay time of 12 h. The RQ is controlled towards a value of 1 by turning the feed pump on and off.
After an inoculation time of 36 h, the RQ starts dropping sharply (Fig. 1). When it hits 1, the pump starts feeding glucose. During the duration of the feed, the RQ oscillates between 0.9 and 1.1.
This is caused by a delay in measurement of the exhaust gas components, as the bioreactor’s exhaust gas needs to pass the additional tubing between the reactor and the GA4 before being measured. This can be further minimized by optimization of the controller’s PID settings.
The end of the batch phase of a fed-batch culture is often indicated by a DO-spike. At this point, the carbon source within the initial culture medium is consumed, the metabolic activity of the culture and, therefore, its oxygen demand drop rapidly, resulting in a sharp increase of DO in the medium. We took advantage of this DO-spike to trigger an automatic start of the feed pump using an automatic programming script. The details are described in the Eppendorf Application Note 439 [3].
Automatic RQ control by programmed feeding
As stated before, the RQ value can serve as an indicator for which substrate is used by the culture. We implemented a software script which starts automatically after inoculation [3]. After a delay time of 12 h, the RQ value of 1 is used to start the feeding pump, and further feeding is automatically controlled based on the RQ value.
Results
We ran P. pastoris fed-batch fermentation two times. In one setup, the feed was started automatically by a script which was triggered by a DO-spike. In the other setup, we implemented a constant RQ-controlled feeding strategy.
The DO-spike based feeding was started once the value of dissolved oxygen raised from 30 % to above 38 % which was the case after 39 h inoculation time [3]. The RQ-controlled feeding was started after a delay time of 12 h. The RQ is controlled towards a value of 1 by turning the feed pump on and off.
After an inoculation time of 36 h, the RQ starts dropping sharply (Fig. 1). When it hits 1, the pump starts feeding glucose. During the duration of the feed, the RQ oscillates between 0.9 and 1.1.
This is caused by a delay in measurement of the exhaust gas components, as the bioreactor’s exhaust gas needs to pass the additional tubing between the reactor and the GA4 before being measured. This can be further minimized by optimization of the controller’s PID settings.
Read more
Read less
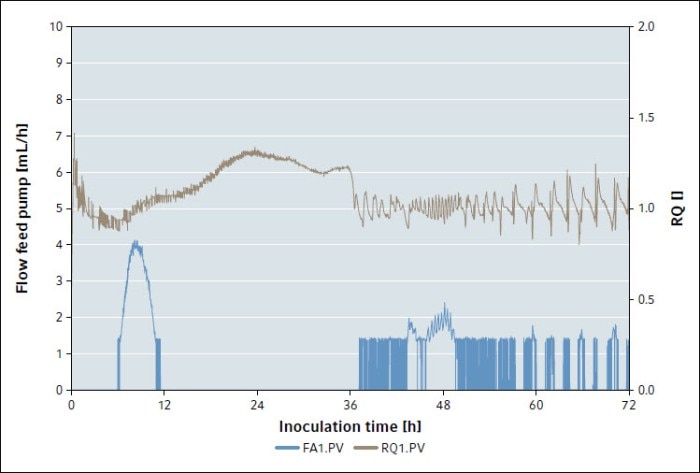
Fig. 1: Fermentation graphs of the flow of the feed pump (blue) and the respiratory quotient (brown) during P. pastoris fermentation with RQ-controlled feeding
During the batch phase, before feed start, the culture’s growth in both settings was comparable (Fig. 2).
After the batch growth phase of the culture, the RQ-controlled feeding resulted in a much earlier exponential growth than the DO-spike triggered feeding. After 56 h, the DO-spike based fed-batch culture reached an OD600 of 245, while the RQ-controlled culture reached an OD600 of 280. The RQ-controlled culture reached an OD600 above 200 at an earlier time point during fermentation than the DO-controlled culture.
After the batch growth phase of the culture, the RQ-controlled feeding resulted in a much earlier exponential growth than the DO-spike triggered feeding. After 56 h, the DO-spike based fed-batch culture reached an OD600 of 245, while the RQ-controlled culture reached an OD600 of 280. The RQ-controlled culture reached an OD600 above 200 at an earlier time point during fermentation than the DO-controlled culture.
Read more
Read less
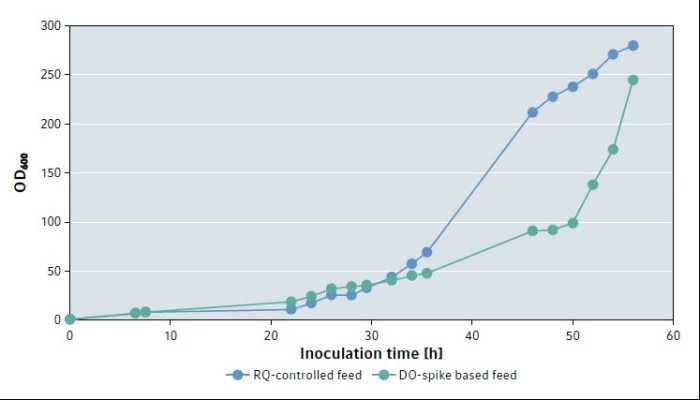
Fig. 2: Growth curves of P. pastoris with RQ-controlled feed and DO-spike based feed
Conclusion
We demonstrated the implementation of a constant RQ-controlled feeding strategy using DASware® Control 5 and a DASbox fermentation system. If the culture’s growth profile and biomass accumulation is an indication of a successful fermentation, it can be concluded that the feeding based on constant RQ has multiple benefits. We observed an OD600 of 200 much earlier with the RQ-based feeding strategy compared to the DO-spike triggered feeding strategy.
This can be explained by insufficient feeding in the DO-spike triggered setup. The feed steps would need to be adapted, which is not the case for the RQ-based feeding. In the latter case, the feeding optimization is automatically self-achieved as the culture creates its own demand for feeding based on the drop of RQ value.
This will save additional experiments and therefore material costs, labor costs, system occupancy, and time.
Literature
[1] Xiong Z. Q., Guo M. J., Guo Y. X., Chu J., Zhuang Y. P., Wang N. S., & Zhang S. L. (2010). Enzyme and Microbial Technology, 46(7), 598–602. https://doi.org/10.1016/j.enzmictec.2010.03.003
[2] Clarke K. G. (2013). 8 - (K. G. B. T. - B. E. Clarke Ed.; pp. 147–170). Woodhead Publishing. https://doi.org/10.1533/9781782421689.147
[3] Schrand N., Schneider M., Sha M. (2021) Eppendorf Application Note 439.
Note: Eppendorf SE reserves the right to modify its products and services at any time. This Application Note is subject to change without notice. Although prepared to ensure accuracy, Eppendorf SE assumes no liability for errors, or for any damages resulting from the application or use of this information. Viewing Application Notes alone cannot as such provide for or replace reading and respecting the current version of the operating manual.
We demonstrated the implementation of a constant RQ-controlled feeding strategy using DASware® Control 5 and a DASbox fermentation system. If the culture’s growth profile and biomass accumulation is an indication of a successful fermentation, it can be concluded that the feeding based on constant RQ has multiple benefits. We observed an OD600 of 200 much earlier with the RQ-based feeding strategy compared to the DO-spike triggered feeding strategy.
This can be explained by insufficient feeding in the DO-spike triggered setup. The feed steps would need to be adapted, which is not the case for the RQ-based feeding. In the latter case, the feeding optimization is automatically self-achieved as the culture creates its own demand for feeding based on the drop of RQ value.
This will save additional experiments and therefore material costs, labor costs, system occupancy, and time.
Literature
[1] Xiong Z. Q., Guo M. J., Guo Y. X., Chu J., Zhuang Y. P., Wang N. S., & Zhang S. L. (2010). Enzyme and Microbial Technology, 46(7), 598–602. https://doi.org/10.1016/j.enzmictec.2010.03.003
[2] Clarke K. G. (2013). 8 - (K. G. B. T. - B. E. Clarke Ed.; pp. 147–170). Woodhead Publishing. https://doi.org/10.1533/9781782421689.147
[3] Schrand N., Schneider M., Sha M. (2021) Eppendorf Application Note 439.
Note: Eppendorf SE reserves the right to modify its products and services at any time. This Application Note is subject to change without notice. Although prepared to ensure accuracy, Eppendorf SE assumes no liability for errors, or for any damages resulting from the application or use of this information. Viewing Application Notes alone cannot as such provide for or replace reading and respecting the current version of the operating manual.
Read more
Read less