MENU
DE | EUR
-
-
-
-
- Forum Labo 2025
- Advanced Therapies Week (ATW) 2025
- SLAS Europe 2025
- Bioprocessing Summit Europe 2025
- Medlab Middle East 2025
- SLAS International 2025
- Biologics World Nordics 2025
- ASIA LABEX: The Lab Show 2025
- BioProcess International Europe 2025
- ISEV 2025
- Future Labs Live 2025
- DataHow Symposium 2025
- Cell 2025
- LabDays 2025
- ILMAC 2025
- ASIA LABEX: The Lab Show 2025
- Stem Cell Community Day 2025
- Nordic Life Science Days 2025
-
-
-
-
- Forum Labo 2025
- Advanced Therapies Week (ATW) 2025
- SLAS Europe 2025
- Bioprocessing Summit Europe 2025
- Medlab Middle East 2025
- SLAS International 2025
- Biologics World Nordics 2025
- ASIA LABEX: The Lab Show 2025
- BioProcess International Europe 2025
- ISEV 2025
- Future Labs Live 2025
- DataHow Symposium 2025
- Cell 2025
- LabDays 2025
- ILMAC 2025
- ASIA LABEX: The Lab Show 2025
- Stem Cell Community Day 2025
- Nordic Life Science Days 2025
DE | EUR
-
- Benchtop Centrifuges
- Floor-Standing Centrifuges
- Refrigerated Centrifuges
- Microcentrifuges
- Multipurpose Centrifuges
- High-Speed Centrifuges
- Ultracentrifuges
- Concentrator
- IVD Products
- High-Speed and Ultracentrifuge Consumables
- Centrifuge Tubes
- Centrifuge Plates
- Device Management Software
- Sample and Information Management
-
- All Pipettes, Dispensers & Automated Liquid Handlers
- Mechanical Pipettes
- Electronic Pipettes
- Multi-Channel Pipettes
- Positive Displacement Pipettes & Dispensers
- Automated Pipetting
- Bottle-Top Dispensers
- Pipette Controllers
- Pipette Tips
- Automation Consumables
- Dispenser & Pipette Accessories
- Automation Accessories
- Dispenser & Pipette Services
Sorry, we couldn't find anything on our website containing your search term.
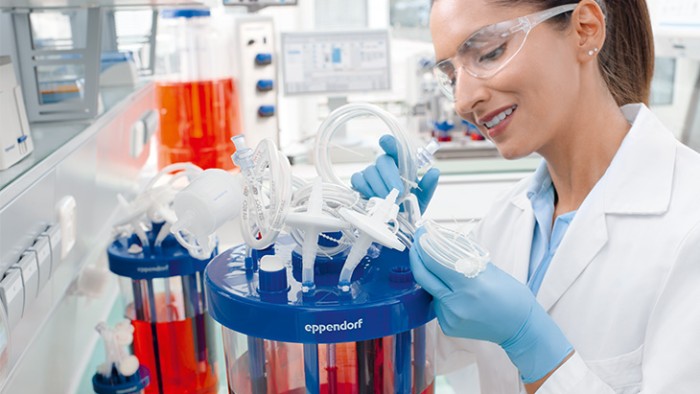
Measuring the kLa (Oxygen Volumetric Mass Transfer Coefficient) of Cell Culture Bioreactors
Igor Vassilev and Ma Sha Lab Academy
- Bioprocessing
- Cell Culture
- Bioprocess
- Essay
The protocol outlines the procedure for measuring kLa of cell culture bioreactors using the gassing out method.
Eppendorf Bioprocess Center and Eppendorf, Inc.
Abstract
The volumetric mass transfer coefficient (kLa) describes the transfer rate of a gas from the gas phase into the bioreactor medium. In aerobic bioprocess applications, kLa is a critical parameter for the evaluation of the efficiency of a bioreactor in terms of how effectively oxygen is supplied to the cultured organism. This short protocol describes the detailed procedure of how to measure kLa of the Eppendorf cell culture bioreactors via the gassing-out method. The kLa values are influenced by many factors such as the reactor and impeller geometry, medium characteristics, and reactor operation (especially agitation and gassing). The change of a single factor will result in a change of the kLa value. As an example, this protocol describes the oxygen kLa measurement of BioBLU® 1c Single-Use Bioreactors at an impeller tip speed range between 0.1 and 1 meter per second (m/s) and a gassing rate between 5 and 60 standard liters per hour (sL/h). For instance, at 0.5 m/s and 25 sL/h the BioBLU 1c with one impeller shows a kLa value of 5.39 ± 0.38 h-1 .
This short protocol can serve as a reference for the bioprocess professionals who are interested in kLa measurement of the large collection of Eppendorf cell culture bioreactors.
A protocol for OTR measurement of fermentation bioreactors is also available.
This short protocol can serve as a reference for the bioprocess professionals who are interested in kLa measurement of the large collection of Eppendorf cell culture bioreactors.
A protocol for OTR measurement of fermentation bioreactors is also available.
Read more
Read less
Table of contents
Read more
Read less
Introduction: What is kLa and how to determine it
What is kLa
The volumetric mass transfer coefficient (kLa) is a parameter that describes the efficiency of the gas-liquid mass transfer in a bioreactor. The ‘kL’ is expressed as the rate of molecular diffusion through the gas-liquid interface area ‘a’ per liquid volume. The kLa is defined by the geometrical properties of the reactor and the operational process aspects. It is a powerful parameter to provide information about gas supply limitations in a bioreactor, in particular for oxygen in aerobic processes. The kLa values can be used for comparison of the performance of bioreactors with similar designs or scale-up strategies [1]. The parameter is important for DO control in bioreactors .How to determine the bioreactor kLa
Several methods using reagents or organisms were developed to measure kLa values [2]. This protocol describes the gassing-out method recommended by the German Society for Chemical Engineering and Biotechnology (DECHEMA) which is an easy and relatively quick method without the need for hazardous chemicals or organisms [3].As organisms are not needed in this cost-effective method, the experiments can be carried out under non-sterile conditions and without medium exchange for several experiments. It is suggested to use 1 × phosphate-buffered saline (PBS) buffer at 37 °C as a closer representation of cell culture medium than water. The method is based on dynamic measurements of oxygen concentration. The first step includes the establishment of anaerobic conditions by gassing the PBS buffer with nitrogen. Next, nitrogen gassing is stopped, the reactor headspace is replaced with air (21 % oxygen), and the PBS buffer is sparged with air at certain flow rates of interest. By monitoring the dissolved oxygen concentration in the PBS buffer as it rises from the minimum to its equilibrium value, the kLa value can be calculated. Removing excess nitrogen from the headspace before the actual kLa measurement ensures defined atmospheric conditions in the headspace and reliable preconditions for kLa measurements [3].
This short protocol is designed mainly to measure kLa values of cell culture bioreactors with typical small kLa values as the measurement is done under slow agitation and low gassing rates to mimic real cell culture conditions with minimized shear stress. To provide readers with realistic examples, the short protocol also includes the determination and comparison of kLa values of BioBLU 1c Single-Use Bioreactors with one impeller (Figure 1).
Read more
Read less
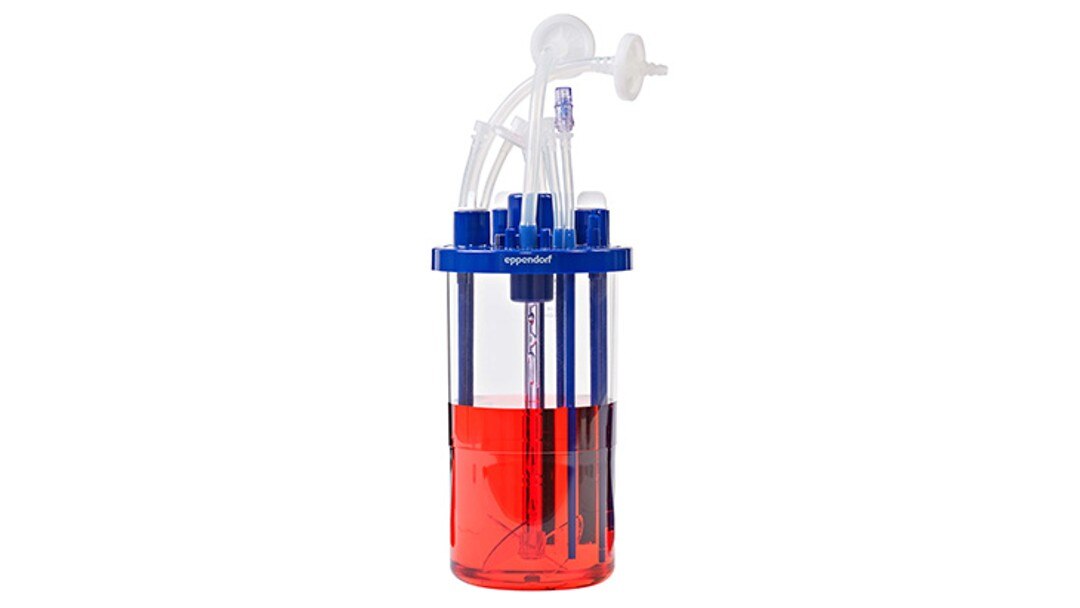
Figure 1A: BioBLU 1c Single-Use Bioreactors were used for kLa measurement in combination with the DASGIP® Parallel Bioreactor System to control the relevant bioprocesss parameters (Figure 1B).
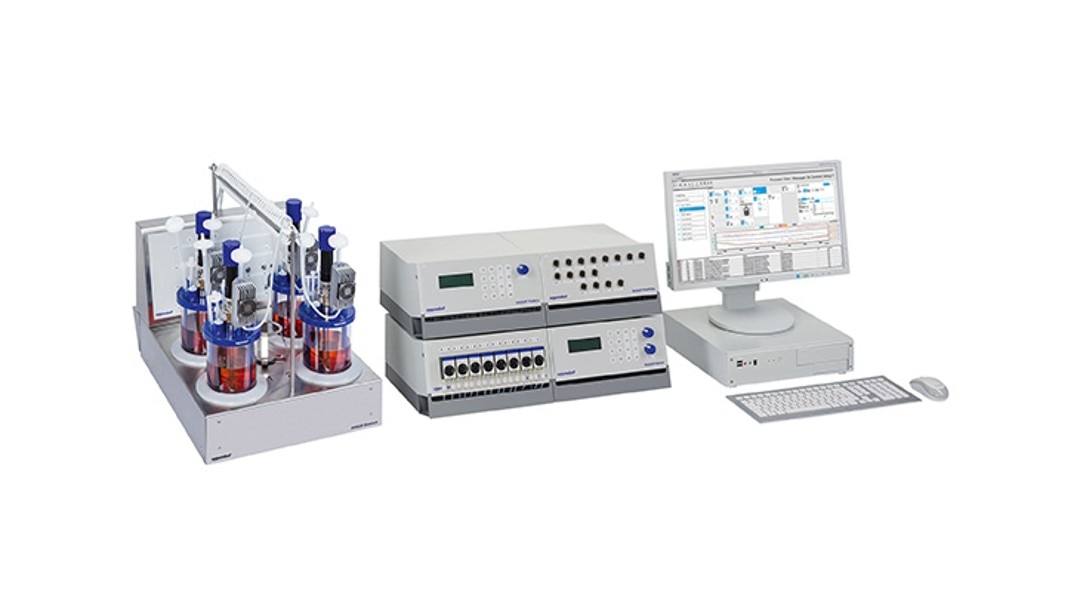
Figure 1B: DASGIP® Parallel Bioreactor System used for kLa measurement of the BioBLU 1c Single-Use Bioreactor (Figure 1A). control the relevant bioprocesss parameters (Figure 1B).
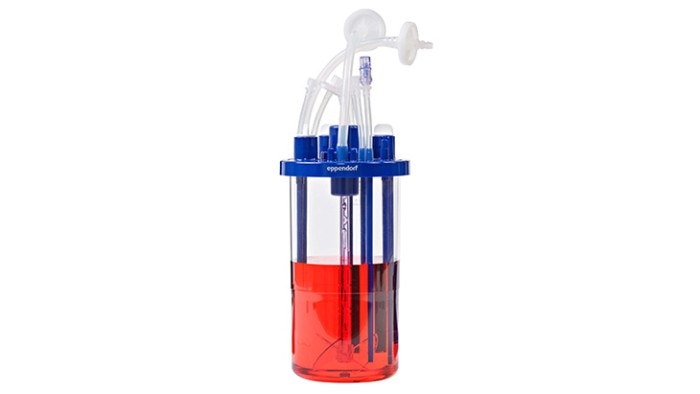
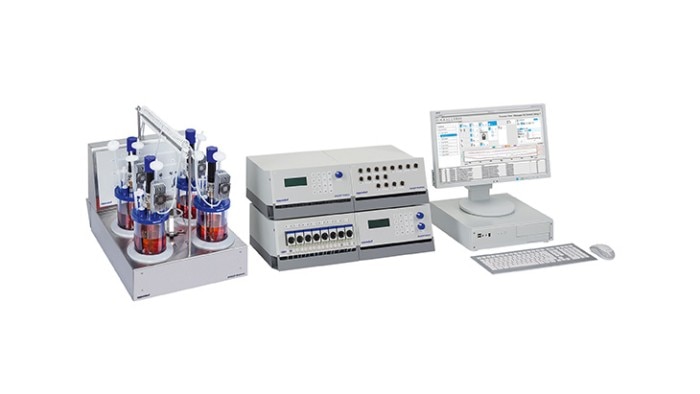
Materials and chemicals used in this study
Equipment
The protocol can be used for either an Eppendorf autoclavable glass bioreactor or a BioBLU Single-Use Bioreactor . In this example, we used a BioBLU 1c Single-Use Bioreactor with one impeller with a DASGIP Bioblock including a DASGIP TC4SC4-B module for cell culture with a agitation speed range of 30 – 1,250 rpm, DASGIP PH4PO4RD4L sensor module and a DASGIP MX4/4 module with an air gassing range of 0.5 – 250 sL/h. Alternatively to the modular system, a BioFlo® 320 can also serve as a controller for kLa measurements. For high gassing accuracy, a thermal mass flow controller for cell culture applications with a gassing range of 0.12 – 60 sL/h (0.002-1.0 SLPM) is recommended to be used with the BioFlo 320 bioprocess controller. In this example, we used Hamilton® OxyFerm FDA 225 Analog polarographic DO sensors (12mm diameter with 225 mm insertion depth). Furthermore, the SciVario® twin equipped with the DASware® control software can serve as an additional alternative bioprocess controller.Chemicals
Phosphate Buffered Saline tablets were used for 1 × PBS medium preparation (Gibco PBS-Tablets, Thermo Fisher Scientific).Read more
Read less
Experimental procedures for kLa measurement
Bioreactor assembly
Assemble the glass bioreactor according to the user manual or take a ready-to-use BioBLU Single-Use Bioreactor. Fill the bioreactor with 1 × PBS to its maximum working volume.DO sensor calibration
Install the appropriate polarized analog DO sensor onto the bioreactor head plate and calibrate the sensor. Set the temperature at 37 °C and agitation at the maximum agitation rate of the bioreactor recommended by the user manual. Sparge gas composed of 100 % nitrogen into the bioreactor at the maximum gassing rate of the bioreactor control system. When DO reading stabilizes, set zero (0 %). Then change the gas composition to sparge 100 % air into the bioreactor at 1 vessel volume per minute (vvm) or at the maximum gassing rate of the bioreactor control system, and wait for the DO reading to stabilize to set the span (100 %).kLa measurement for oxygen of Eppendorf cell culture bioreactors
Keep the temperature at 37 °C and agitation of the bioreactor at the maximum agitation rate recommended by the user manual. Sparge gas composed of 100 % nitrogen into the bioreactor at the maximum gassing rate of the bioreactor control system until the DO values drop below 10 %. Thereafter, stop agitating or set agitation to the minimum setpoint of the used controller, and flush the head space with 100 % air at 0.05 vvm via overlay gassing until the gas in the headspace has been exchanged at least three times. Continue headspace gassing and start data acquisition with a control software. Immediately start agitation and submerged gassing with 100 % air at impeller tip speeds and gassing rates of interest depending on needs, controller selection and bioreactor choice. For example, when using a BioBLU 1c Single-Use Bioreactor with a DASGIP Bioblock, the impeller tip speed and gassing rate can range from 0.1 to 1 m/s, and from 1 to 60 sL/h, respectively. The measurement can be stopped when the DO measuring reaches values over 90 %. Carry out the experiment at least three times to provide a mean kLa of the bioreactor ideally with a standard deviation below 10 %. Repeat the kLa measurements under a broad range of process operation conditions varying gassing rates and agitation to evaluate the behavior of kLa at different cell culturing conditions. The experimental conditions of selected examples are summarized in Table 1.Read more
Read less
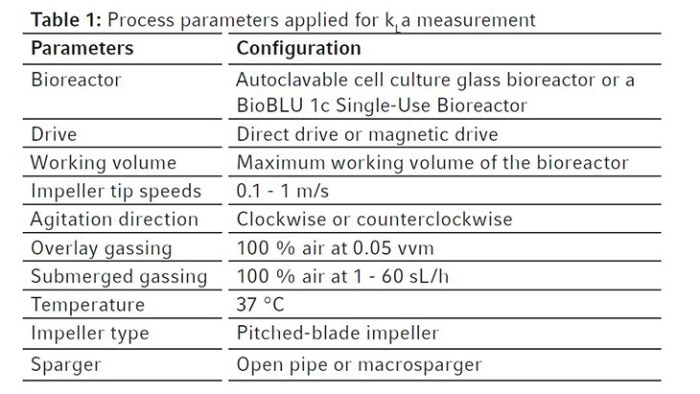
Table 1: Process parameters applied for kLa measurement
Calculation of kLa
The kLa of oxygen in a bioreactor is calculated using the following formulars [3] where DO(t0) is equal to the minimum dissolved oxygen content in the medium (i.e., 0 %) and DO* represents DO at saturation (i.e., 100 %). DO(t) is the measured DO content (%) in the liquid at each time point t (h). The kLa value is determined by plotting a linear graph using the left side of equation 3 as y-axis values as a function of time with a minimum of seven values between 10 and 90 % DO. The kLa value equals the absolute value of the slope of the graph (Figure 2).
Read more
Read less

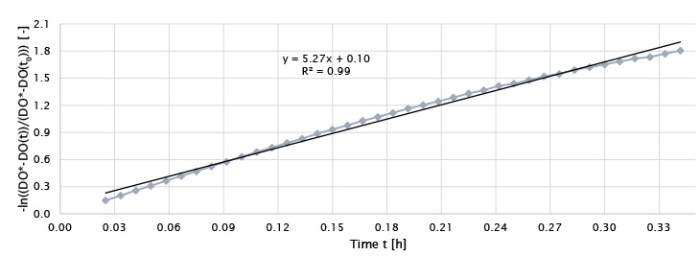
Figure 2: An example (BioBLU 1c with one impeller, 0.5 m/s, 25 sL/h) of plotting the left side of Equation 3 -ln((DO*-DO(t))/(DO*-DO(t0))) as a function of time to determine the kLa value. The absolute slope of the graph (5.27) represents the kLa value with h-1 as its unit.
Example of kLa measurement using BioBLU 1c Single-Use Bioreactors with one impeller
The ready-to-use BioBLU 1c Single-Use Bioreactor was set up as described in the user manual and filled to its maximum working volume with 1 × PBS (i.e. 1250 mL). A polarized Hamilton OxyFerm FDA 225 analog polarographic DO sensor with a diameter of 12 mm and a 225 mm insertion depth was installed in the bioreactor and calibrated via a two-point calibration as follows: the temperature was set to 37 °C, impeller tip speed was set to 600 rpm (1.57 m/s) in clockwise agitation direction, and 100 % nitrogen submerged gassing was set to 75 sL/h. After reaching a stabilized DO, the zero point (0 %) was set. Then the gassing was changed to 60 sL/h and gas content to 100 % air. The DO calibration was finalized by setting the span when the DO reading stabilized (100 %).
The oxygen kLa of the bioreactors was determined at gassing rates of 5, 10, 25 and 60 sL/h, and impeller tip speeds of 0.1, 0.2, 0.5 and 1 m/s. The process of the kLa determination method can be divided into three phases (Table 2).
The oxygen kLa of the bioreactors was determined at gassing rates of 5, 10, 25 and 60 sL/h, and impeller tip speeds of 0.1, 0.2, 0.5 and 1 m/s. The process of the kLa determination method can be divided into three phases (Table 2).
Read more
Read less
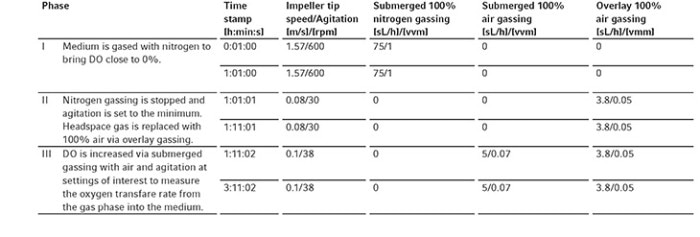
Table 2: Time profile of the different phases to measure kLa at 0.1 m/s tip speed and 5 sL/h air gassing
At the beginning of each kLa measurement (phase I), the DO was first brought close to 0 % by gassing the medium with 100 % nitrogen at 75 sL/h (the DASware control time profile of nitrogen gassing can be seen in Figure 3A) and 600 rpm (1.57 m/s) impeller tip speed (the DASware control time profile of agitation can be seen in Figure 3B). In phase II, the nitrogen gassing was stopped and agitation was set to the minimum of the controller (i.e., to 0.08 m/s tip speed using the DASGIP Bioblock with the DASGIP TC4SC4-B module). The headspace gas of the reactor was replaced with 100 % air by overlay gassing with air at 0.05 vvm for 10 min (the DASware control time profile of overlay gassing can be seen in Figure 3C). Afterward (phase III), submerged gassing (100 % air at 5 sL/h) was initiated (the DASware control time profile of submerged gassing can be seen in Figure 3D) and overlay gassing was continued at 0.05 vvm. The agitation was immediately started at 0.1 m/s tip speed. The DO changes were recorded every 30 seconds via DASware control, and data acquisition was completed when DO readings reached values over 90 %. The measured DO values during DO raise between 10 and 90% were used to determine kLa by plotting the left side of equation 3 as a function of time. Depending on the linear regression, the chosen spectrum of measured DO values can be adjusted to a range between 10 and 75 % to ensure linear slopes with high R-squared (R2 >0.99) (Figure 2).
Read more
Read less
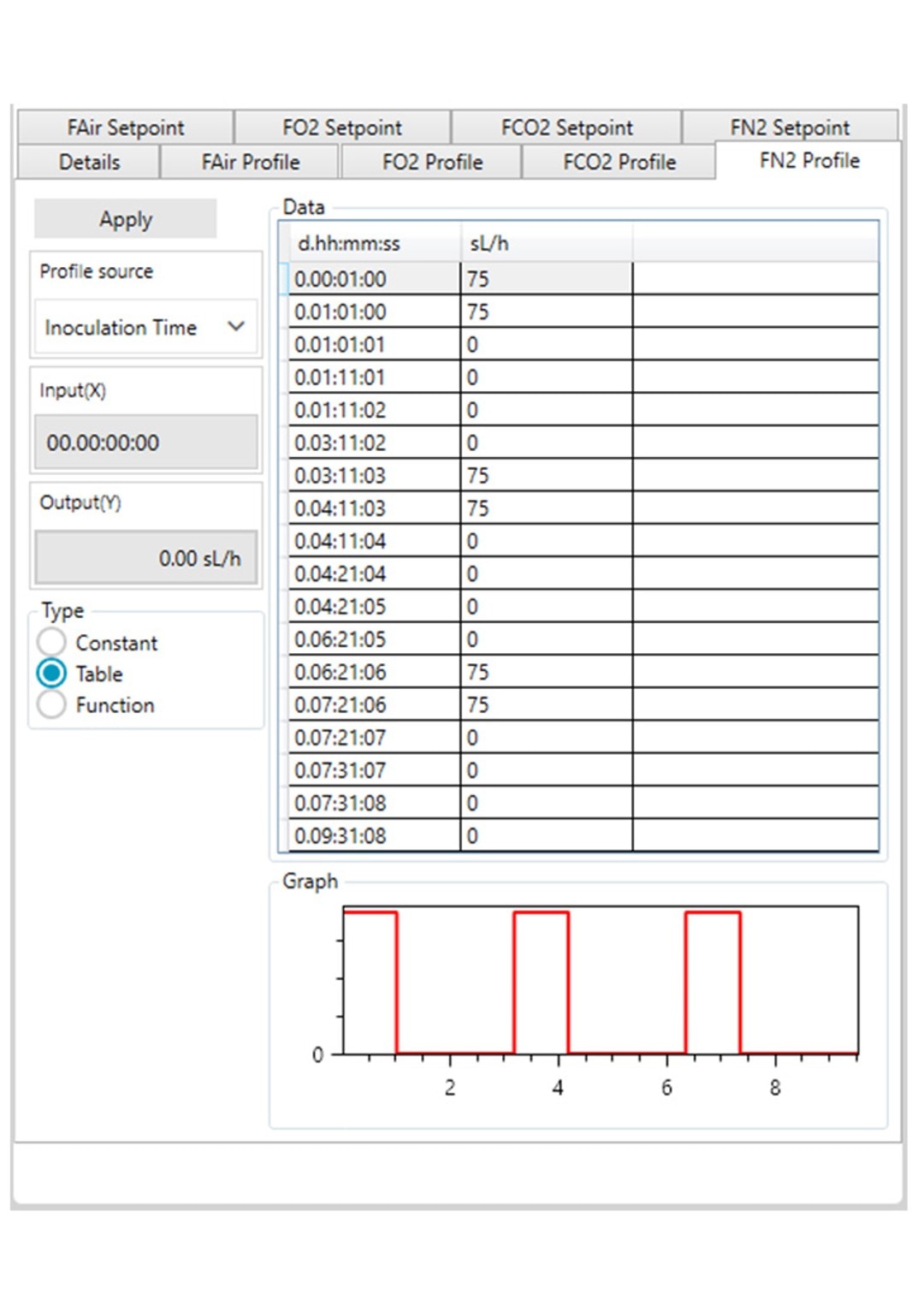
Figure 3: DASware control time profile to measure kL a in triplicates at 0.1 m/s tip speed and 5 sL/h air gassing. A: Submerged nitrogen gassing.
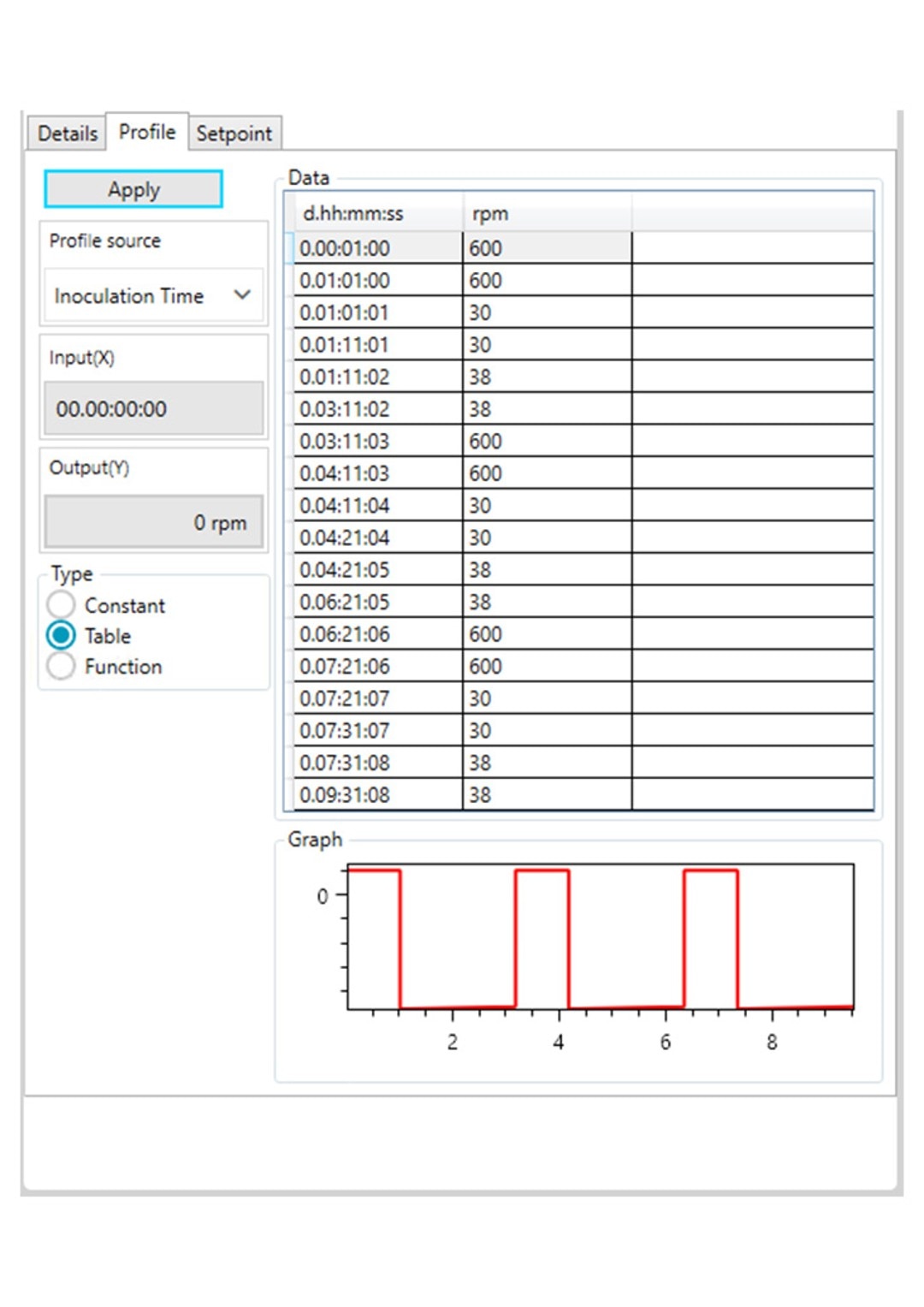
Figure 3: DASware control time profile to measure kLa in triplicates at 0.1 m/s tip speed and 5 sL/h air gassing. B: Agitation.
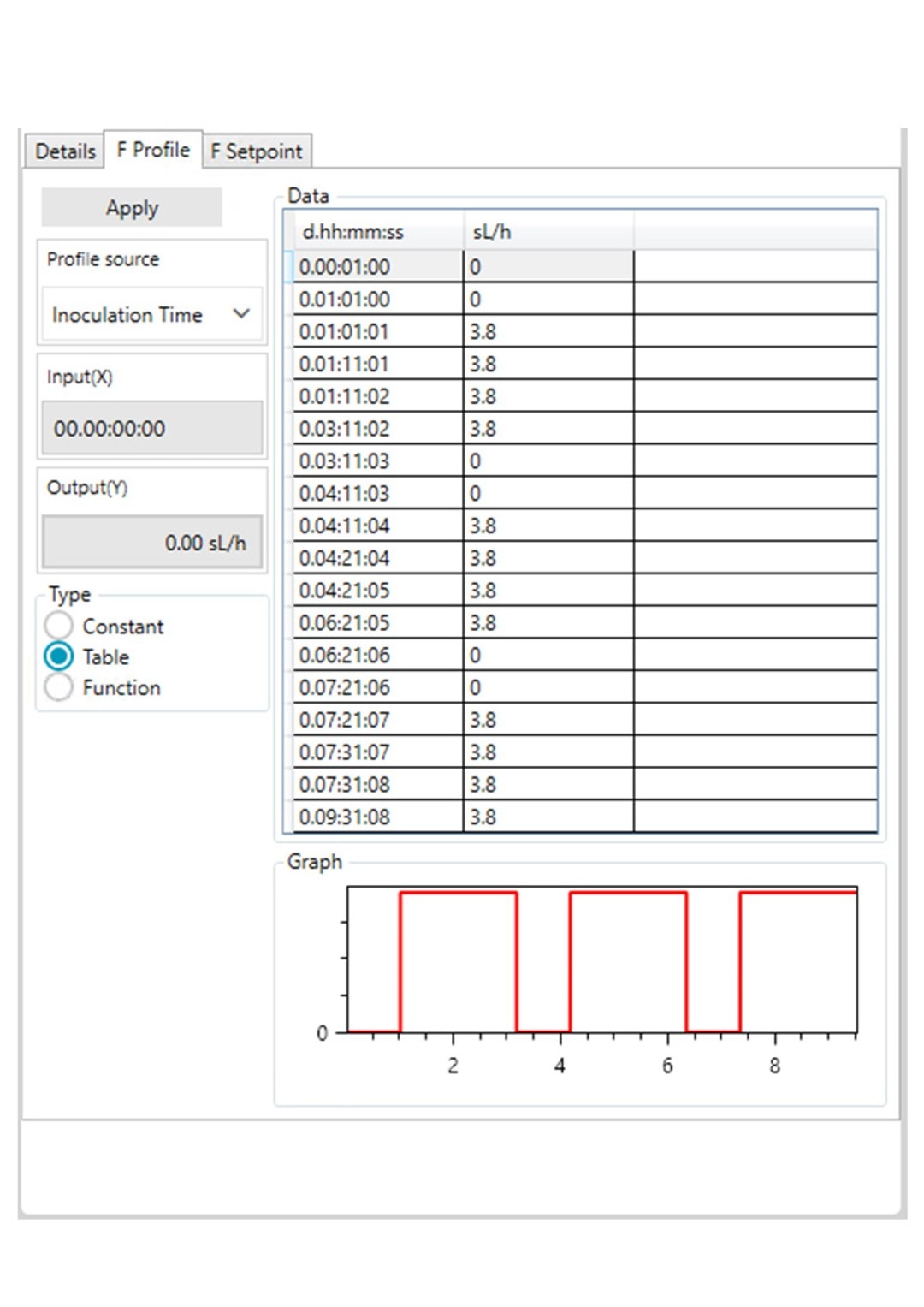
Figure 3: DASware control time profile to measure kLa in triplicates at 0.1 m/s tip speed and 5 sL/h air gassing. C: Overlay air gassing.
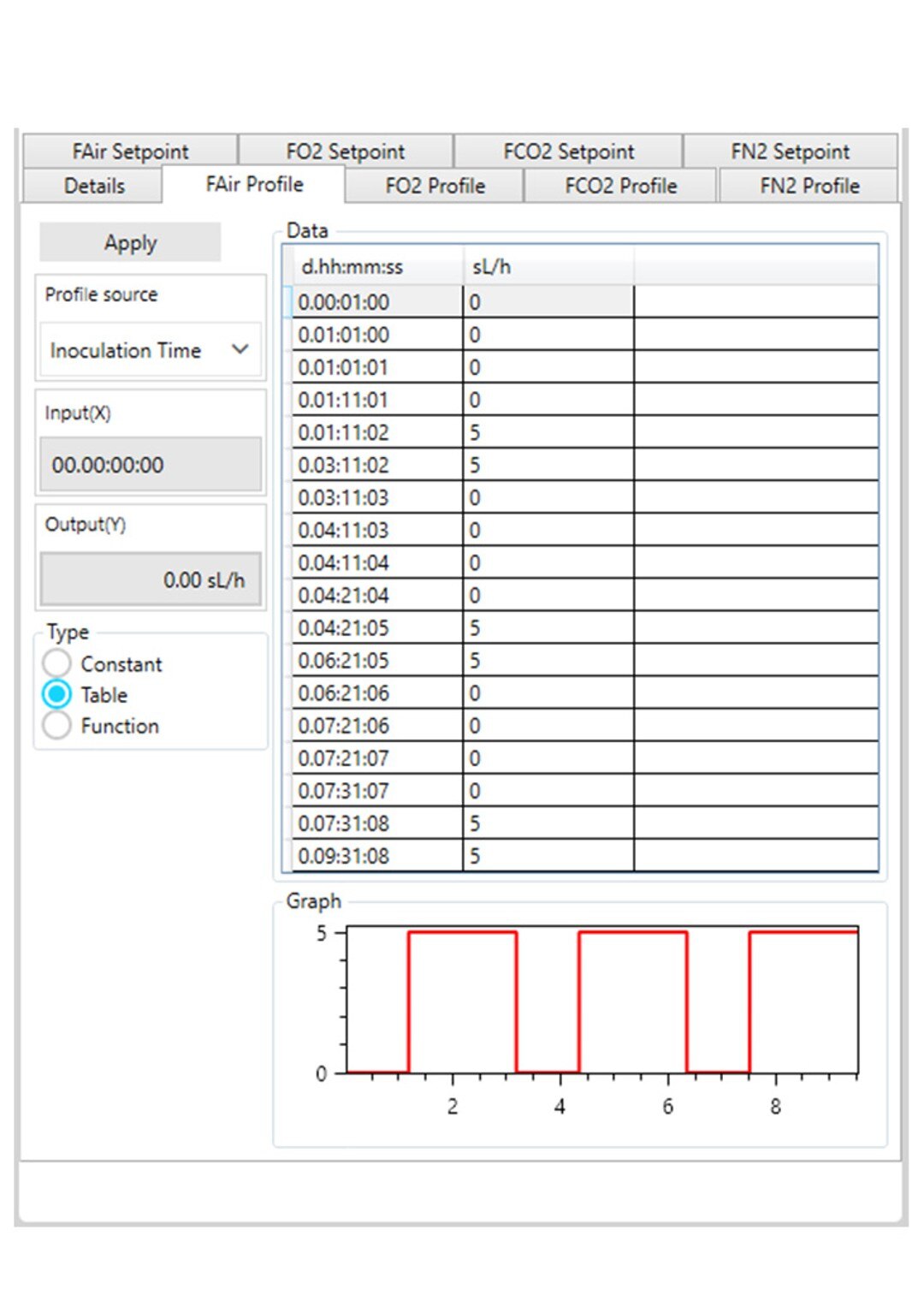
Figure 3: DASware control time profile to measure kLa in triplicates at 0.1 m/s tip speed and 5 sL/h air gassing. D: Submerged air gassing.
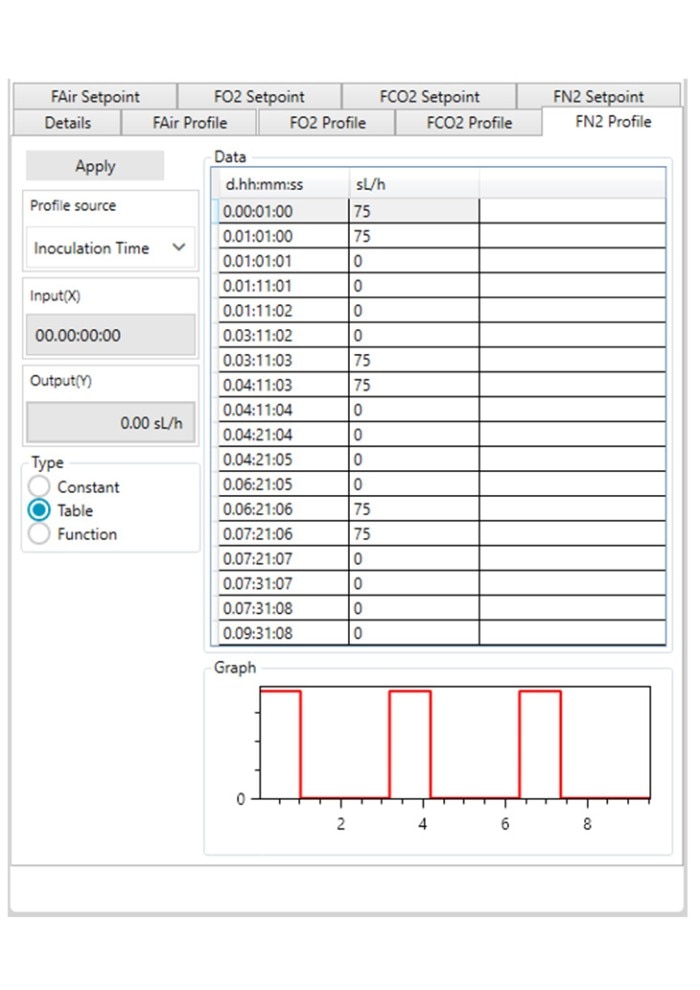
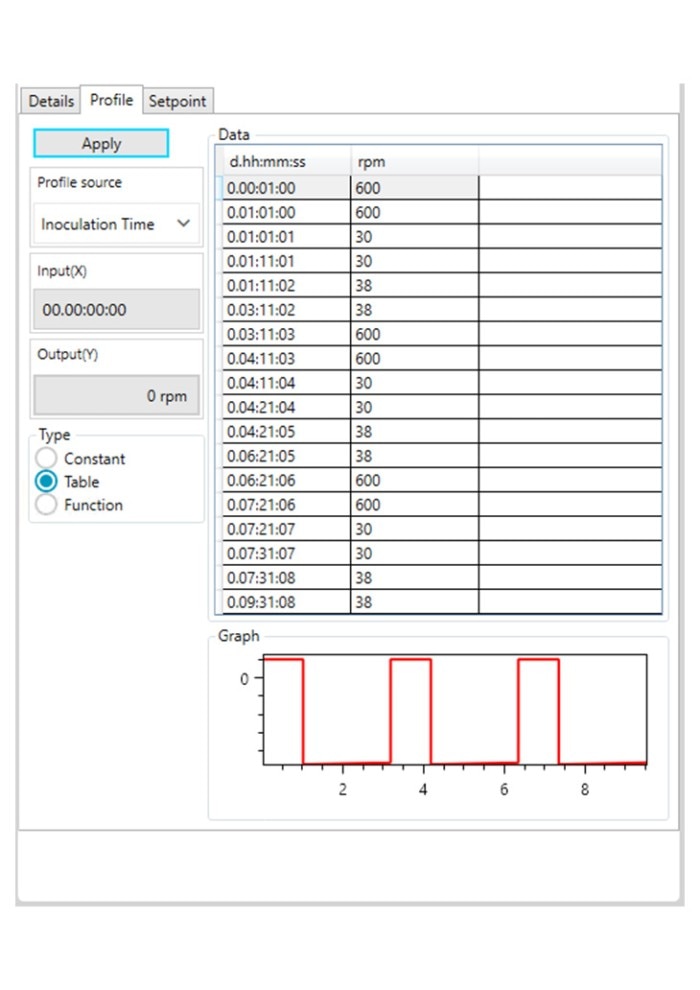
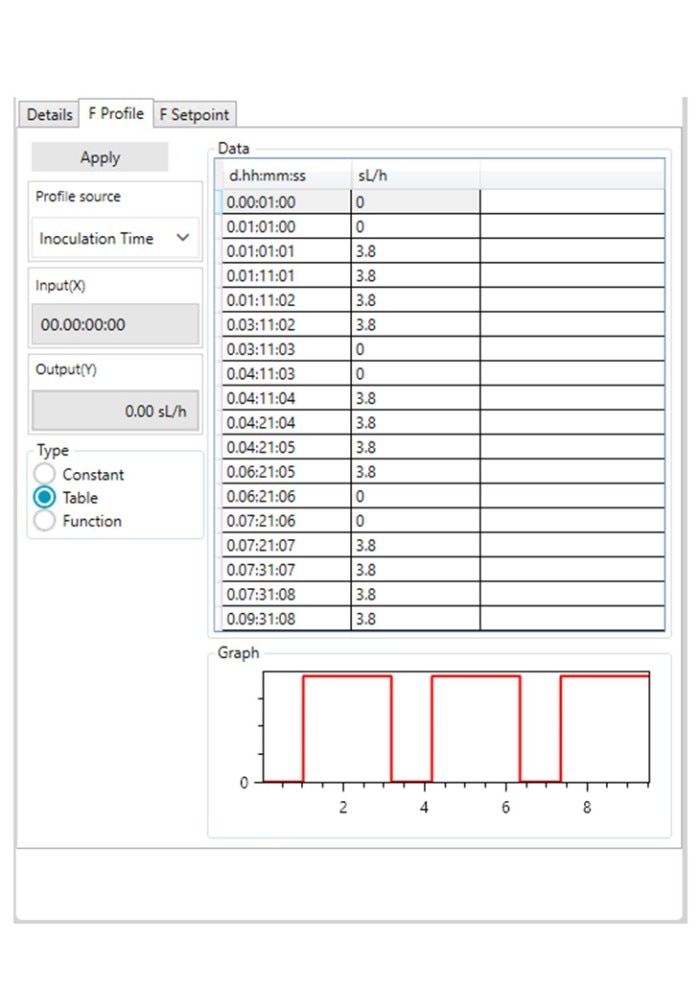
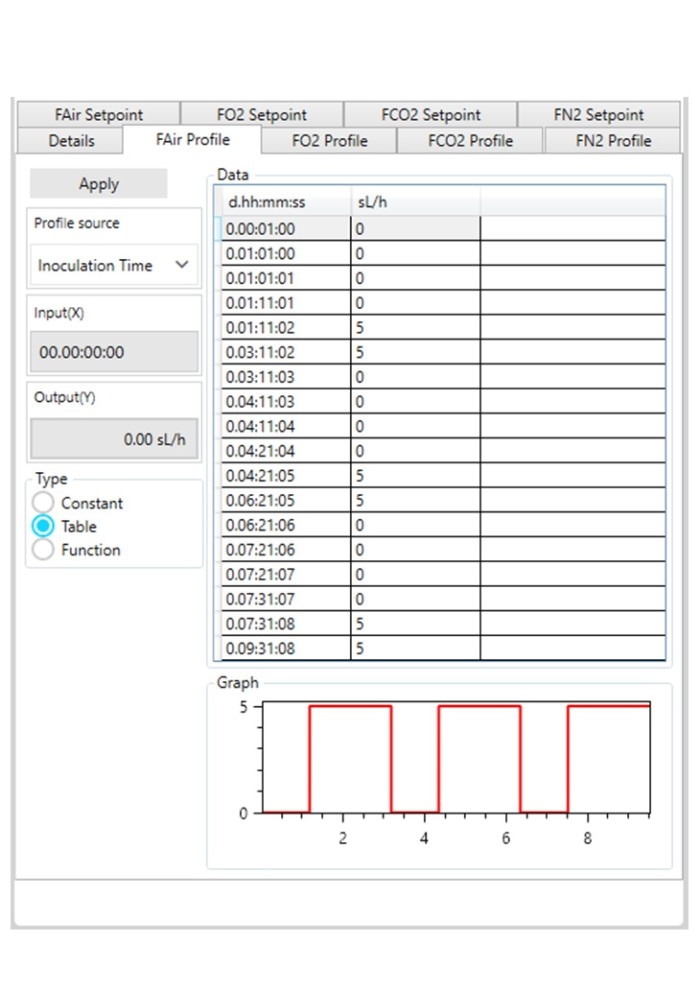
However, ensure to use a statistically significant number of DO values (n > 7). All three phases need to be repeated in the order listed in Table 2 at least three times (Figure 3) to provide a mean kLa of the bioreactor at the set impeller tip speed and gassing rate (i.e., 0.1 m/s and 5 sL/h). In this example, a DASGIP Bioblock with DASware control was applied to regulate the process and record DO data (Figure 3). Alternatively, a BioFlo 320 bioprocess controller could directly be used for process control, data recording and data reading. Figure 4 demonstrates an example of time profiles for submerged nitrogen gassing, agitation, overlay air gassing, and submerged air gassing using the BioFlo 320 controller interface.
Read more
Read less
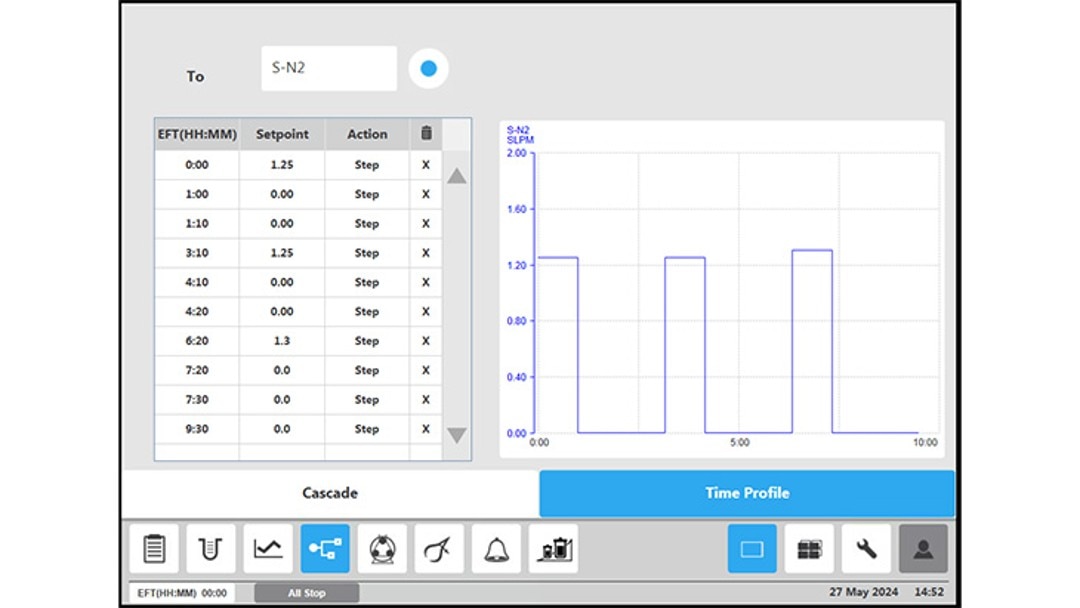
Figure 4: BioFlo 320 bioprocess controller time profile to measure kLa in triplicates at 0.1 m/s tip speed and 5 sL/h air gassing. (A) Submerged nitrogen gassing.
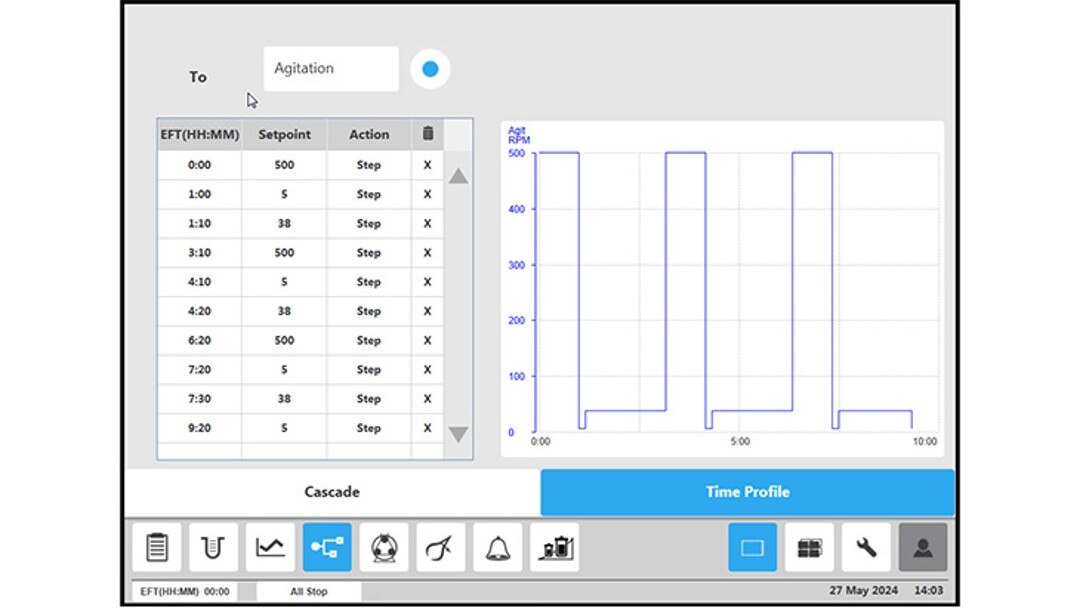
Figure 4: BioFlo 320 bioprocess controller time profile to measure kLa in triplicates at 0.1 m/s tip speed and 5 sL/h air gassing. (B) agitation.
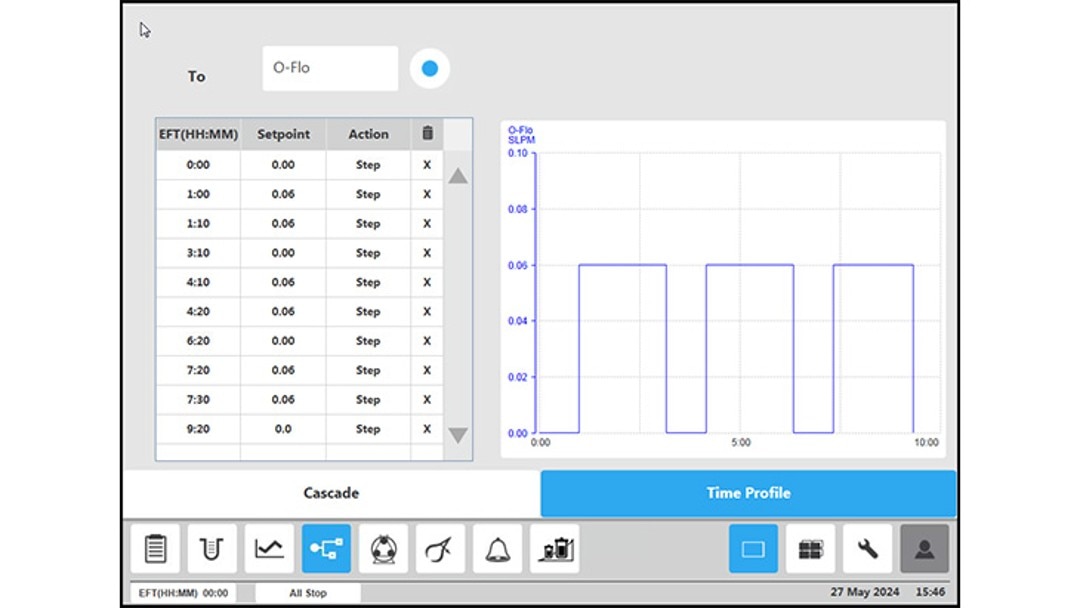
Figure 4: BioFlo 320 bioprocess controller time profile to measure kLa in triplicates at 0.1 m/s tip speed and 5 sL/h air gassing. (C) overlay air gassing.
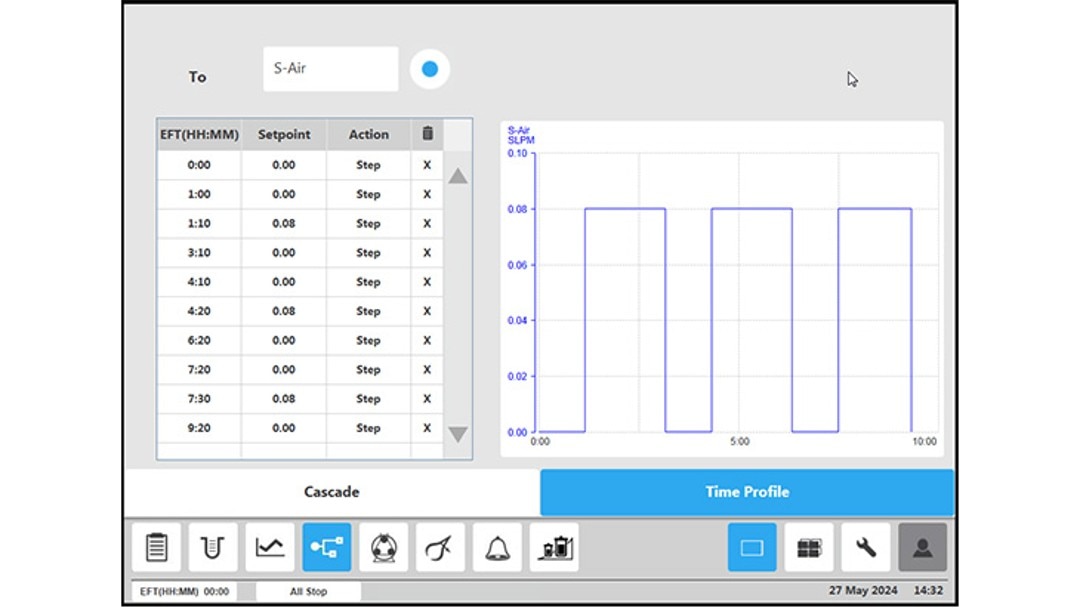
Figure 4: BioFlo 320 bioprocess controller time profile to measure kL a in triplicates at 0.1 m/s tip speed and 5 sL/h air gassing. (D) submerged air gassing.
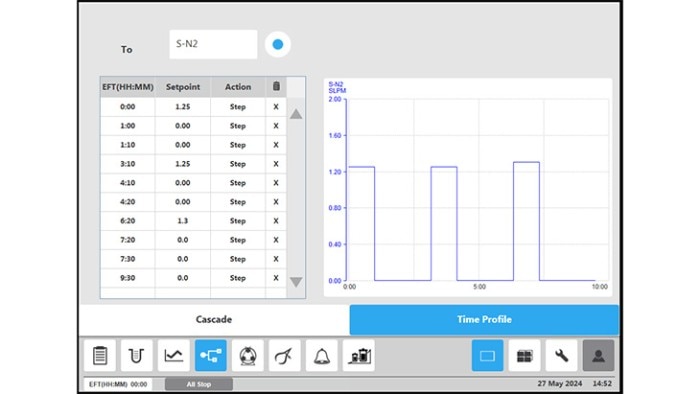
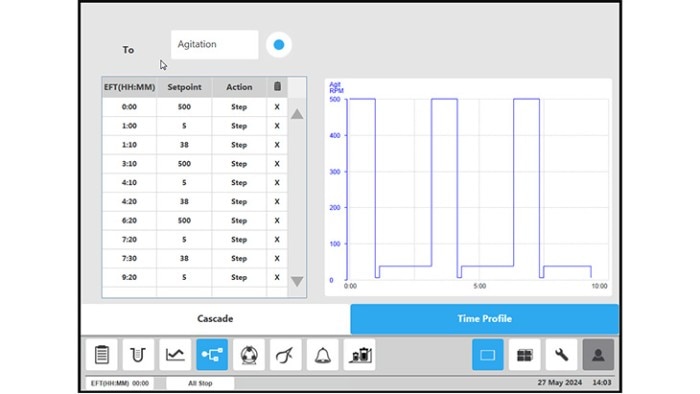
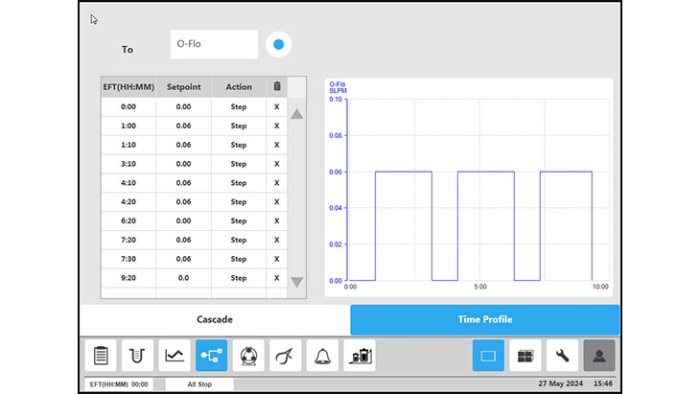
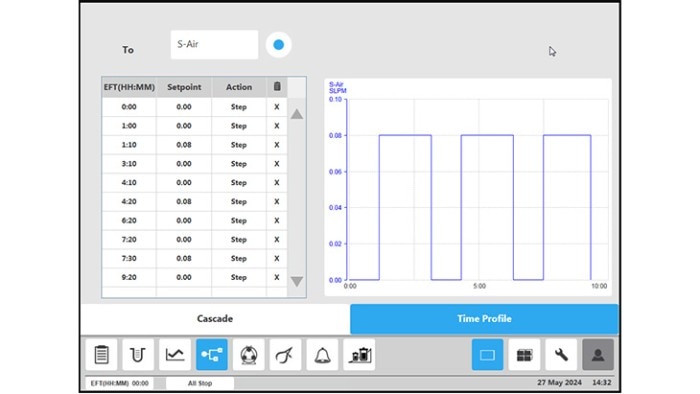
All procedure steps were repeated for each impeller tip speed (i.e., 0.1, 0.2, 0.5 and 1 m/s) and each gassing rate (5, 10, 25 and 60 sL/h). Table 3 and Figure 5 summarize the kLa values measured in triplicates at the different operation conditions. The determined oxygen kLa values of the BioBLU 1c Single-Use Bioreactors grew with increasing gassing flow rates and agitation. The kLa values ranged from 2.06 ± 0.02 to 5.39 ± 0.38 h-1 at impeller tip speeds between 0.1 and 0.5 m/s and gassing rates between 5 and 25 sL/h. That process operation range covers most mammalian cell culture needs. Higher impeller tip speeds and gassing rates, e.g. 1 m/s and 60 sL/h respectively, led to a greater kLa increase. However, such operation parameters do not represent common mammalian cell cultivation conditions due to greater shear stress for the cells.
The impeller tip speed zone of 0.1 – 0.5 m/s can be used to compare the kLa values of BioBLU Single-Use Bioreactors with different volumes from small to bench scale. For example, the determined kLa values of the BioBLU 1c are comparable and overlap with the kLa values of BioBLU 0.3c (max. working volume 0.25 L), 3c (max. working volume 3.75 L) and 50c (max. working volume 40 L), which allows the use of constant kLa between different sized vessels as a strategy for cell culture scale-up [4].
The impeller tip speed zone of 0.1 – 0.5 m/s can be used to compare the kLa values of BioBLU Single-Use Bioreactors with different volumes from small to bench scale. For example, the determined kLa values of the BioBLU 1c are comparable and overlap with the kLa values of BioBLU 0.3c (max. working volume 0.25 L), 3c (max. working volume 3.75 L) and 50c (max. working volume 40 L), which allows the use of constant kLa between different sized vessels as a strategy for cell culture scale-up [4].
Read more
Read less

Table 3: Measured kLa values of oxygen of the BioBLU 1c Single-Use Bioreactor at impeller tip speeds of 0.1 – 1 m/s and gassing rates of 5 – 60 sL/h.
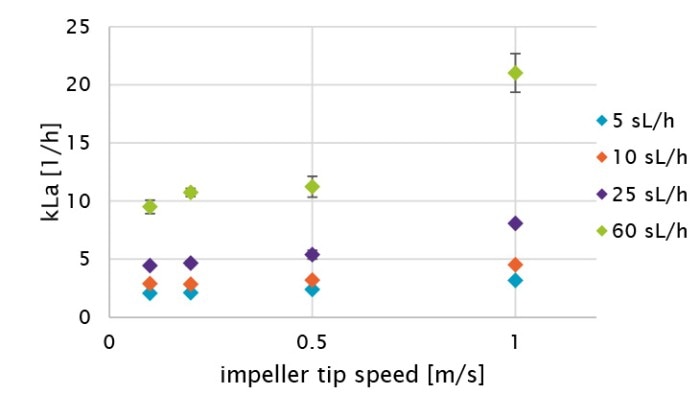
Figure 5: Graphical comparison of oxygen kLa values of the BioBLU 1c Single-Use Bioreactor at different impeller tip speeds and air gassing rates (see Table 3).
Discussion
kLa is an important parameter describing the capacities of a bioreactor to transfer gas into the bioreactor medium and can be used for scale-up strategies. Several methods exist to determine kLa values and different methods may lead to varying kLa values of the same bioreactor [2]. This short protocol introduces a well-accepted kLa determination method, which is accurate, easy, cost-effective, safe, sustainable, and environmentally friendly.
The short protocol presented here is based on DECHEMA recommendations, in which a headspace gas exchange is recommended to reduce the residual nitrogen concentration in the gassing phase and thereby, ensure a more precise measurement of the oxygen transfer [3]. This short protocol provides an example for users to plot out their own graphs for the calculation of kLa. Alternatively, users can also use a web-based table offered by DECHEMA to automatically calculate the kLa values [3].
In summary, this short protocol describes a reliable and reproducible method for measuring the kLa value of a bioreactor. It can serve as a reference for the bioprocess professionals who are interested in kLa measurements of the large collection of bioreactors within the Eppendorf portfolio including reusable glass and single-use bioreactors of different volumes from small to bench scale.
The short protocol presented here is based on DECHEMA recommendations, in which a headspace gas exchange is recommended to reduce the residual nitrogen concentration in the gassing phase and thereby, ensure a more precise measurement of the oxygen transfer [3]. This short protocol provides an example for users to plot out their own graphs for the calculation of kLa. Alternatively, users can also use a web-based table offered by DECHEMA to automatically calculate the kLa values [3].
In summary, this short protocol describes a reliable and reproducible method for measuring the kLa value of a bioreactor. It can serve as a reference for the bioprocess professionals who are interested in kLa measurements of the large collection of bioreactors within the Eppendorf portfolio including reusable glass and single-use bioreactors of different volumes from small to bench scale.
Read more
Read less
Literature
[1] Garcia-Ochoa, F., Gomez, E. (2009). Bioreactor scale-up and oxygen transfer rate in microbial processes: an overview. Biotechnology advances, 27(2), 153-176.
[2] Aroniada, M., Maina, S., Koutinas, A., Kookos, I. K. (2020). Estimation of volumetric mass transfer coefficient (kLa) - Review of classical approaches and contribution of a novel methodology. Biochemical Engineering Journal, 155, 107458.
[3] Bauer, I., Dreher, T., Eibl, D., Glöckler, R., Husemann, et al. (2020). Recommendations for process engineering characterisation of single-use bioreactors and mixing systems by using experimental methods. DECHEMA Gesellschaft für Chemische Technik und Biotechnologie eV.
[4] Han, X. K., Willard, S., Sha, M. (2016). Cell Culture Scale-Up in BioBLU® c Rigid-Wall, Single-Use Bioreactors. Eppendorf Poster. http://cellculturedish.com/wp-content/uploads/sites/2/2020/05/Poster_BioBLU_Cell-Culture-Scale-U_ eng.pdf [17.05.2024]
[2] Aroniada, M., Maina, S., Koutinas, A., Kookos, I. K. (2020). Estimation of volumetric mass transfer coefficient (kLa) - Review of classical approaches and contribution of a novel methodology. Biochemical Engineering Journal, 155, 107458.
[3] Bauer, I., Dreher, T., Eibl, D., Glöckler, R., Husemann, et al. (2020). Recommendations for process engineering characterisation of single-use bioreactors and mixing systems by using experimental methods. DECHEMA Gesellschaft für Chemische Technik und Biotechnologie eV.
[4] Han, X. K., Willard, S., Sha, M. (2016). Cell Culture Scale-Up in BioBLU® c Rigid-Wall, Single-Use Bioreactors. Eppendorf Poster. http://cellculturedish.com/wp-content/uploads/sites/2/2020/05/Poster_BioBLU_Cell-Culture-Scale-U_ eng.pdf [17.05.2024]
Read more
Read less
Methods are intended for research applications. They are not intended, verified or validated for use in the diagnosis of disease or other human health conditions.
Eppendorf SE reserves the right to modify its products and services at any time. This short protocol is subject to change without notice. Although prepared to ensure accuracy, Eppendorf SE assumes no liability for errors, or for any damages resulting from the application or use of this information. Viewing the short protocol alone cannot as such provide for or replace reading and respecting the current version of the operating manual.
Eppendorf SE reserves the right to modify its products and services at any time. This short protocol is subject to change without notice. Although prepared to ensure accuracy, Eppendorf SE assumes no liability for errors, or for any damages resulting from the application or use of this information. Viewing the short protocol alone cannot as such provide for or replace reading and respecting the current version of the operating manual.
Read more
Read less