MENU
CH | CHF
-
-
-
- Services pour bioprocédés
- Services pour centrifugeuse et rotors
- Services pour Mastercycler
- Services pour automates de pipetage
- Services pour congélateurs
- Services pour incubateurs
- Services pour agitateurs
- Services pour appareils de photométrie
- Service de contrôle de la température et de l’agitation
- Service pour pipette
-
-
-
-
- Services pour bioprocédés
- Services pour centrifugeuse et rotors
- Services pour Mastercycler
- Services pour automates de pipetage
- Services pour congélateurs
- Services pour incubateurs
- Services pour agitateurs
- Services pour appareils de photométrie
- Service de contrôle de la température et de l’agitation
- Service pour pipette
-
CH | CHF
-
- Centrifugeuses de paillasse
- Centrifugeuses au sol
- Centrifugeuses réfrigérées
- Microcentrifugeuses
- Centrifugeuses multi-fonctions
- Centrifugeuses haute vitesse
- Ultracentrifugeuses
- Concentrateur
- Produits IVD
- High-Speed and Ultracentrifuge Consumables
- Tubes de centrifugeuse
- Plaques de centrifugeuse
- Gestion des appareils
- Gestion des échantillons et des informations
-
- Pipetage manuel & distribution
- Pipettes mécaniques
- Pipettes électroniques
- Pipettes multicanaux
- Distributeurs et pipettes à déplacement positif
- Automates de pipetage
- Distributeurs sur flacon
- Auxiliaires de pipetage
- Pointes de pipette
- Consommables d’automatisation
- Accessoires pour pipettes et distributeurs
- Accessoires d’automatisation
- Services pour pipettes et distributeurs
Sorry, we couldn't find anything on our website containing your search term.
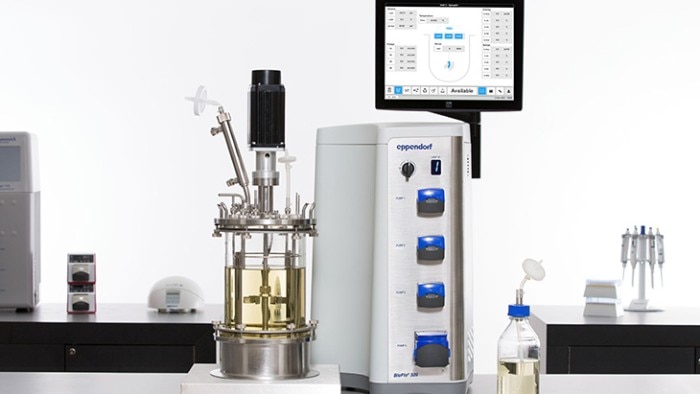
Measuring the Oxygen Transfer Rate (OTR) of Fermentation Bioreactors
Ying Yang, Marcus Deinstadt, and Ma Sha Lab Academy
- Bioprocédés
- Culture de microorganismes
- Bioprocédés
- Cuves
- Test
The protocol outlines the procedure for determining OTR of fermentation bioreactors using the sulfite depletion method.
Eppendorf, Inc. Enfield, CT USA
Abstract
This short protocol describes the detailed procedure of how to measure the oxygen transfer rate (OTR) of the Eppendorf fermentation bioreactors. OTR is often listed as one of the bioreactor specifications and describes the rate of oxygen delivery from gas into liquid. It is important to measure OTR under industry standard conditions with 1 vessel volume per minute (VVM) of air sparging only, with no oxygen enrichment. Higher VVM or oxygen sparging will significantly inflate OTR values. In this protocol, we used the industry standard sulfite depletion method for our measurement under air sparging and maximum agitation. As an example, we took a BioFlo® 320 3 L glass bioreactor to demonstrate the process. We calculated the average OTR to be 366.3 mmol O2/(L x h). We also compared OTR measurements when using different types of dissolved oxygen (DO) sensors.
This short protocol can serve as a reference for the bioprocess professionals who are interested in OTR measurement of the large collection of Eppendorf fermentation bioreactors.
A protocol for kLa measurement of cell culture bioreactors is also available.
This short protocol can serve as a reference for the bioprocess professionals who are interested in OTR measurement of the large collection of Eppendorf fermentation bioreactors.
A protocol for kLa measurement of cell culture bioreactors is also available.
Lire moins
Introduction: What is OTR and how to determine it
What is the oxygen transfer rate
The oxygen transfer rate (OTR) describes the rate of oxygen delivery from gas into liquid such as an agitated suspension culture in a bioreactor. The typical unit for OTR is mmol O2/(L x h), i.e., the amount of oxygen transferred into one liter of culture per hour. OTR is a very important parameter of fermentation bioreactors which affects dissolved oxygen control in bioreactors and which affects the selection, design, and scale-up of a bioprocess [1].The OTR of a bioreactor provided by most manufacturers represents the maximum oxygen transfer capability of this specific bioreactor under one VVM air sparging. There are many factors that affect the bioreactor’s OTR including the physical properties of the gas and liquid, operating conditions, and geometric characteristics of the bioreactor.
The mass transfer of oxygen is usually a limiting factor in aerobic fermentation bioprocesses. Under oxygen limitation, cell growth and product formation can be affected [2]. To assess their oxygen transfer capabilities, the Eppendorf applications team determined the OTR of many fermentation bioreactors.
Determining OTR using the sulfite depletion method
Here in this short protocol, we describe in detail how we measure the OTR of an Eppendorf fermentation bioreactor [3]. We use the industry standard sulfite depletion method for our measurement [1]. Maximum agitation and 1 VVM air flow provide oxygen transfer to the system. With the addition of sodium sulfite (Na2SO3), oxygen then rapidly reacts as the oxidizing agent to generate sodium sulfate (Na2SO4) in the presence of the copper catalyst.
Lire moins
The chemical reaction is shown here:

Since the oxygen entering the solution is immediately consumed to oxidize sulfite into sulfate, the reaction rate of sulfite oxidation represents the oxygen transfer rate of the bioreactor. OTR can be calculated by measuring the recovery of the dissolved oxygen (DO) in the bioreactor after sodium sulfite depletion. To demonstrate the process, we used a BioFlo 320 3 L glass bioreactor as an example to calculate its OTR. We also compared the performance of different DO sensors in the process. We compared an analog polarographic sensor from Mettler-Toledo® , a digital Mettler-Toledo ISM® polarographic sensor, and a digital Mettler-Toledo ISM optical sensor to evaluate if there was a difference in response rate for OTR measurements. For this experiment a BioFlo 320 5 L glass bioreactor was used.
Lire moins
Materials used in this protocol
Equipment
- An Eppendorf autoclavable glass bioreactor or a BioBLU® f Single-Use Bioreactor . In this study, we used a 3 L and a 5 L autoclavable glass bioreactor with stainless-steel dished bottom and direct drive for BioFlo 320.
- BioFlo 320 control station
- Mettler Toledo analog polarographic DO sensor (12 mm diameter with 220 mm insertion depth)
- Mettler Toledo analog polarographic DO sensor (12 mm diameter with 320 mm insertion depth)
- Mettler Toledo ISM polarographic DO sensor (12 mm diameter with 320 mm insertion depth)
- Mettler Toledo ISM optical DO sensor (12 mm diameter with 320 mm insertion depth)
Chemicals
- Sodium sulfite anhydrous (Na2SO3, Fisher Scientific® , S430-10)
- Copper(II) sulfate pentahydrate (CuSO4·5H2O) solution at 80 g/L concentration (J.T. Baker, 1843)
Other materials
- Weigh dish, lab balance, stopwatch, funnel, transfer pipettes, Easypet® 3 electronic pipette controller.
Lire moins
Experimental procedures for OTR measurement
Bioreactor assembly
Assemble the glass bioreactor as per the user manual or take a ready-to-use BioBLU f Single-Use Bioreactor. Fill the bioreactor with deionized (DI) water to its maximum working volume.DO sensor calibration
Install a DO sensor in the bioreactor. Calibrate the sensor as described in Short Protocol 40 [4].OTR determination
We kept the temperature at 30 °C and sparged gas at 1 VVM with 100 % air. The experimental conditions are summarized in Table 1.
Lire moins
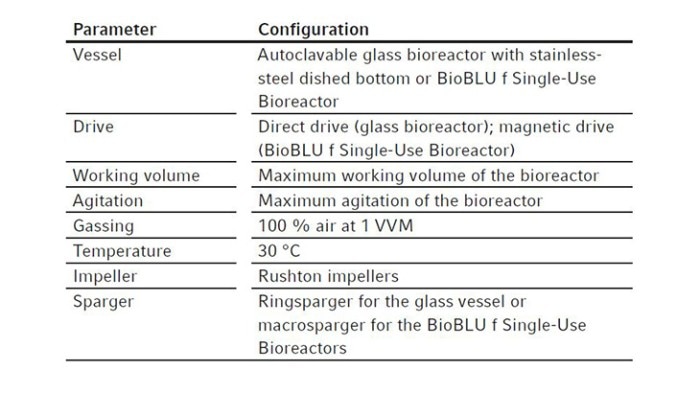
Table 1: Process parameters applied in OTR measurement
At the beginning of the experiment, DO is stable at 100 %. Open a port on the bioreactor head plate and transfer 80 g/L copper sulfate stock solution as the catalyst at a volumetric ratio of 2 mL per 1 L of working volume into the bioreactor. The copper is the reaction catalyst and when added sufficiently, it gives the solution a light blue color. It is important to investigate and if necessary, order fresh chemicals if this color is missing. Weigh Na2SO3 powder and add it all at once to the bioreactor through a funnel as quickly as possible to reach a final Na2SO3 concentration of 11 g/L. Leave the ports used to add chemicals open during the experiment to allow maximum exhaust gas outflow. Some preliminary studies in our lab showed that there is an 8 % decrease in OTR when measured with all ports closed after chemical addition vs. ports left open. Track time from the time point when DO reaches 50 % on the downward trend to the time point when DO bounces back to 50 % on the way up. The completion of DO recovery indicates the exhaustion of the amount of Na2SO3 added to the system (Figure 2). DO control is turned off during the entire experiment, hence, automatic DO control is not used. Read the present values of DO manually on the control interface of BioFlo 320 and track time using a stopwatch or read them through the trend graph auto-collected by the unit. Carry out the experiment twice to provide an average OTR of the bioreactor. The detailed bioreactor setup is illustrated in Figure 3.
Lire moins
The oxygen transfer rate can be calculated using the following equation (WNa2SO3 is the weight of Na2SO3 powder used in the experiment, 126 g/mol is the molecular weight of Na2SO3, and t is the elapsed time in hours tracked for DO recovery):
Lire moins
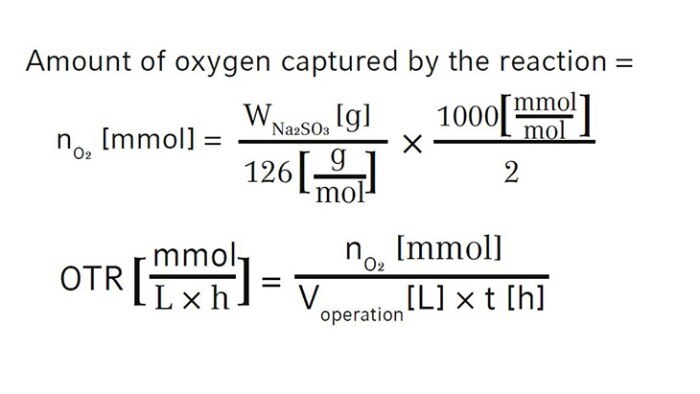
Results
An example of OTR measurement using the 3 L autoclavable glass vessel
We first assembled the 3 L BioFlo 320 fermentation bioreactor as per the user manual and filled the bioreactor with DI water to its maximum working volume which was 3.75 L in this case. Then we installed the polarized analog DO sensor in the bioreactor head plate and calibrated the sensor as follows. We set the temperature at 30 °C and agitation at 1200 rpm which is the maximum agitation rate of the bioreactor recommended by the user manual and sparged gas composed of 100 % nitrogen into the bioreactor at 3.75 SLPM (1 VVM). When DO reading stabilized after 10–30 minutes, zero (0 %) was set. Then we changed the gas composition to sparge 100 % air into the bioreactor at 3.75 SLPM, waited for another 10–30 minutes for the DO reading to stabilize to set the span (100 %). The DO sensor calibration was then completed.We kept the temperature at 30 °C, agitation at 1200 rpm, and gas sparging at 3.75 SLPM with 100 % air for the OTR measurement. At the beginning of the experiment, DO was stable at 100 %. We opened a Pg 13.5 port on the bioreactor head plate and transferred 7.5 mL of the 80 g/L copper sulfate stock solution into the bioreactor as the catalyst. We then weighed 41.25 g Na2SO3 powder and added it to the bioreactor through a funnel as quickly as possible to reach a final Na2SO3 concentration of 11 g/L. The ports were left open after chemical addition. Time was tracked by a stopwatch from the time point when DO reached 50 % on the downward trend to the time point when DO bounced back to 50 % on the way up as shown in Figure 2. We read the present values of DO manually on the control interface of BioFlo 320 or through the trend graph auto-collected by the unit, both at a data logging rate of every 5 seconds. The experiment was carried out twice to provide a mean OTR of this 3 L glass bioreactor. In this duplicated experiment, the elapsed time t we tracked for DO recovery was 427 s and 431 s, corresponding to 0.1186 h and 0.1197 h, respectively. The weight of Na2SO3 powder was 41.25 g. Based on this, using the equations shown above, we calculated the mean OTR to be 366.3 mmol O2/(L x h) for the 3 L autoclavable BioFlo 320 glass bioreactor (Table 2).
Lire moins
DO sensor type comparison for OTR determination
For these experiments, we evaluated different types of DO sensors to compare their performances in OTR measurement. We first assembled a BioFlo 320 5 L fermentation bioreactor as per the user manual and filled it with DI water to its maximum working volume, which is 5.625 L. The sensors were polarized and calibrated together using the process stated previously in Short Protocol 40 [4]. Two experiments were designed for such comparisons.We first compared the analog DO sensor with the digital ISM sensor. We installed the two sensors in the same bioreactor for the experiment, removing the pH sensor to allow for the extra DO sensor in the process. This experiment was repeated three times so an average OTR can be calculated for each sensor. We then ran a second experiment comparing an analog DO sensor with the optical DO sensor. All experimental conditions were set the same as described below. The bioreactor temperature was set to 30 °C and gas sparging was set to 5.625 SLPM corresponding to 1 VVM with 100 % air for the OTR measurement. Agitation was set at the maximum of 1200 rpm. Pg 13.5 ports were opened on the headplate for chemical addition. Then 11.25 mL of the 80 g/L copper sulfate solution were added to the bioreactor, followed by the addition of 61.875 g Na2SO3. The ports were left open after chemical addition. Time was tracked by a stopwatch from the time point when DO reached 50 % on the downward trend to the time point when DO bounced back to 50 % on the way up as shown in Figure 2. The calculated OTRs of the 5 L glass bioreactor using these different DO sensors are shown in the Tables 3 and 4. The averages and standard deviations of these OTR measurements are further illustrated in Figure 4.
Lire moins
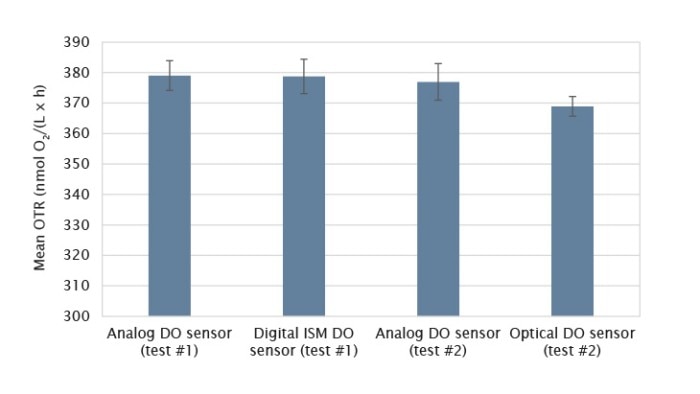
Figure 4: The comparison of 5 L glass bioreactor OTR measurements among analog, digital ISM, and optical DO sensors (each column represents the mean of three independent measurements and the error bar represents the respective standard deviation). Test #1: Analog DO sensor and digital ISM DO sensor were compared. Test #2: Analolg DO sensor and optical DO sensor were compared.
We found that the analog and ISM sensors measured almost identically. For the BioFlo 320 5 L glass bioreactor, the average OTR calculated from the analog and ISM sensor measurements were 379.02 and 378.74 mmol O2/(L x h), respectively. The OTR measurements based on optical DO sensor readings seemed to be slightly lower than the OTR measurements based on analog DO sensor readings, however the differences were not statistically significant.
Lire moins
Discussion
The sulfite depletion method used in this study is a reliable and relatively easy way for OTR determination under nonsterile conditions, although the process can be tedious and for large bioreactors, a great amount of chemicals is required. There can be some human error in time tracking using stopwatch because the data logging was set to be every five seconds and the rate of oxygen depletion and oxygen recovery in this experiment can be relatively fast. However, the error from timing technique can be minimized with practice and the elapsed time can be double checked by studying the trend graph collected by the BioFlo 320 control unit. We find both timing techniques work equally well. When measuring OTR of a specific bioreactor using different types of DO sensors, it seemed that OTR based on optical DO sensor readings were slightly lower compared to OTR based on analog and digital ISM DO sensor readings. We would recommend following this comparison procedure against an analog sensor if using an alternative DO sensor in OTR measurements to ensure accuracy.
In summary, this short protocol describes the method for measuring and calculating OTR of a fermentation bioreactor under industry standard OTR measurement conditions using the sulfite depletion method. A fermentation bioreactor with a high OTR can effectively support robust microbial growth and desired product yield. Therefore, this short protocol can serve as a reference for the bioprocess professionals who are interested in OTR measurement of Eppendorf’s large collection of fermentation bioreactors.
In summary, this short protocol describes the method for measuring and calculating OTR of a fermentation bioreactor under industry standard OTR measurement conditions using the sulfite depletion method. A fermentation bioreactor with a high OTR can effectively support robust microbial growth and desired product yield. Therefore, this short protocol can serve as a reference for the bioprocess professionals who are interested in OTR measurement of Eppendorf’s large collection of fermentation bioreactors.
Lire moins
Literature
[1] Garcia-Ochoa F, Gomez E. Bioreactor scale-up and oxygen transfer rate in microbial processes: An overview. Biotechnology Advances (27), 153–176. 2009
[2] Hall SM. Rules of Thumb for Chemical Engineers (Sixth Edition). 2018
[3] Kelleher B, Nori C, Voll K, Siddiquee K, and Sha M. Evaluation of the BioFlo® 320 process capabilities. Eppendorf Poster. 2014
[4] Willard S. A Guide to Calibration on the BioFlo® 120 and BioFlo® 320: Dissolved Oxygen Sensors. Eppendorf Short Protocol No. 40 . 2017.
[2] Hall SM. Rules of Thumb for Chemical Engineers (Sixth Edition). 2018
[3] Kelleher B, Nori C, Voll K, Siddiquee K, and Sha M. Evaluation of the BioFlo® 320 process capabilities. Eppendorf Poster. 2014
[4] Willard S. A Guide to Calibration on the BioFlo® 120 and BioFlo® 320: Dissolved Oxygen Sensors. Eppendorf Short Protocol No. 40 . 2017.
Lire moins
Methods are intended for research applications. They are not intended, verified or validated for use in the diagnosis of disease or other human health conditions.
Eppendorf SE reserves the right to modify its products and services at any time. This short protocol is subject to change without notice. Although prepared to ensure accuracy, Eppendorf SE assumes no liability for errors, or for any damages resulting from the application or use of this information. Viewing the short protocol alone cannot as such provide for or replace reading and respecting the current version of the operating manual.
Eppendorf SE reserves the right to modify its products and services at any time. This short protocol is subject to change without notice. Although prepared to ensure accuracy, Eppendorf SE assumes no liability for errors, or for any damages resulting from the application or use of this information. Viewing the short protocol alone cannot as such provide for or replace reading and respecting the current version of the operating manual.
Lire moins