MENÜ
DE | EUR
DE | EUR
-
- Tischzentrifugen
- Standzentrifugen
- Gekühlte Zentrifugen
- Mikrozentrifugen
- Mehrzweckzentrifugen
- Hochgeschwindigkeitszentrifugen
- Ultrazentrifugen
- Concentrator
- IVD Produkte
- High-Speed and Ultracentrifuge Consumables
- Zentrifugenröhrchen
- Zentrifugenplatten
- Gerätemanagement
- Proben- und Informationsmanagement
-
- Manuelles Pipettieren & Dispensieren
- Mechanische Pipetten
- Elektronische Pipetten
- Mehrkanalpipetten
- Direktverdrängerpipetten & Dispenser
- Automatisches Pipettieren
- Flaschenaufsatzdispenser
- Pipettierhilfen
- Pipettenspitzen
- Verbrauchsartikel für die Automation
- Zubehör für Dispenser & Pipetten
- Zubehör für die Automation
- Services für Dispenser & Pipetten
Sorry, we couldn't find anything on our website containing your search term.
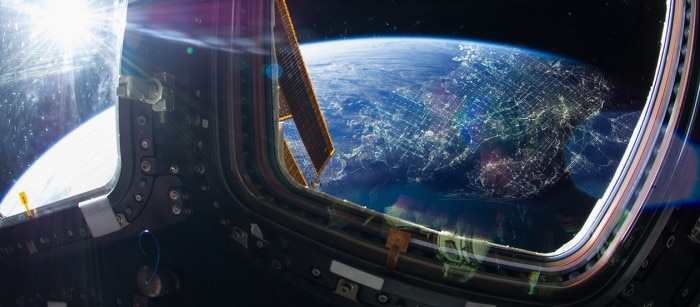
Perfect Project Planning is crucial – anytime and anywhere
Lab Academy
- countonit
- Essay
Sometimes it is helpful to look at what you are doing from a different angle. In this case, we do it right from the very top – from outer space! Do you have any idea how space agencies and astronauts solve the challenges of laboratory work that they face in orbit?
The scientific work on board of a space station is determined by three critical factors: weight, space and time. All three are extremely limited on every mission. Nevertheless, being able to carry out all experiments without errors under these conditions requires creative thinking, perfect planning down to the last detail and a great deal of discipline.
The European Columbus module is a multi-purpose research laboratory permanently attached to the International Space Station. As one of three research modules it provides internal payload accommodation for experiments in the field of multidisciplinary research under zero-gravity conditions. In addition to experiments in gravitational, radiation biology, astrobiology and human physiology, scientists work on projects in basic research, materials science, fluid and solid-state physics as well as plasma research. In Columbus, there is a total capacity for 16 so-called International Standard Payload Racks (ISPR). Ten of those are available for the scientific equipment of various experiments, three serve as storage space and three contain technology for the infrastructure as power and water supply or air conditioning. The racks with the scientific equipment are each designed for one field of research. They have a modular design with slide-in modules so that experiments or equipment can be exchanged quickly. Each rack has its own power supply, cooling systems and, depending on the task, video and data lines.
One of those ISPRs is the Fluid Science Laboratory (FSL), supporting experiments on the dynamics of fluids under conditions of zero gravity. Processes that are normally influenced by gravitational convection, sedimentation, stratification or different pressure conditions can be studied with the FSL. The aim of the experiments is to optimize production processes on earth and to increase the quality of the products. It should make it possible to more accurately calculate and control manufacturing processes that have to take fluids into account, such as metallurgical processing and crystal growth.
How research in space helps improve manufacturing processes on Earth
The European Columbus module is a multi-purpose research laboratory permanently attached to the International Space Station. As one of three research modules it provides internal payload accommodation for experiments in the field of multidisciplinary research under zero-gravity conditions. In addition to experiments in gravitational, radiation biology, astrobiology and human physiology, scientists work on projects in basic research, materials science, fluid and solid-state physics as well as plasma research. In Columbus, there is a total capacity for 16 so-called International Standard Payload Racks (ISPR). Ten of those are available for the scientific equipment of various experiments, three serve as storage space and three contain technology for the infrastructure as power and water supply or air conditioning. The racks with the scientific equipment are each designed for one field of research. They have a modular design with slide-in modules so that experiments or equipment can be exchanged quickly. Each rack has its own power supply, cooling systems and, depending on the task, video and data lines.
One of those ISPRs is the Fluid Science Laboratory (FSL), supporting experiments on the dynamics of fluids under conditions of zero gravity. Processes that are normally influenced by gravitational convection, sedimentation, stratification or different pressure conditions can be studied with the FSL. The aim of the experiments is to optimize production processes on earth and to increase the quality of the products. It should make it possible to more accurately calculate and control manufacturing processes that have to take fluids into account, such as metallurgical processing and crystal growth.
Mehr erfahren
Weniger lesen
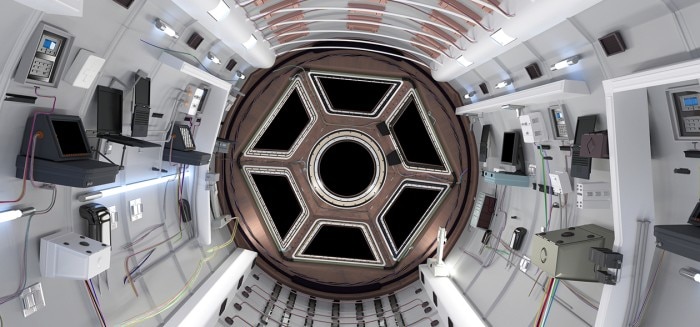
3D Ergonomics – how to use a limited space to its fullest potential
On board of Columbus, every angle is used – but it is used in three dimensions, for storage, instruments and consumables. Because of the zero-gravity conditions, it makes sense to arrange the instruments, work areas and storage compartments of the laboratory three-dimensionally around the astronaut. The radii recommended on Earth for optimal physiological and anatomical working areas are adhered to as far as possible in order to support smooth, fault- and fatigue-free work – but on board the space station this also applies upwards and downwards.
Terrestrial laboratories usually waste a lot of space here – especially in optimal physiological and anatomical working areas, which would be well suited for keeping instruments and materials. It can make a lot of sense to think in spheres here, too: The use of centrifuges that can be pushed under a bench (not used for bench work while sitting) frees up more work space on the bench. Especially when setting up a new laboratory, this provides an opportunity to make the arrangement as ergonomic as possible. Where are the benches located? How much bench space does each member of staff have available? Where are the storage cabinets positioned? How deep are the storage cabinets and what is kept where? Do the laboratory technicians sit at the bench or do they stand? Where are the refrigerator, centrifuge etc. located? This also includes continuous straightening-up so that everything is always in the right place, familiar to everyone.
Perfect planning in advance saves time and trouble
In order to make full use of the time available for experiments and transport capacity, all payloads, workflows and protocols are optimized down to the smallest detail before launch. To save time and eliminate potential errors, all consumables and materials required for each experiment are packed into individual storage bags and clearly labelled.
Optimal preparation of experiments in the form of test kits saves time and increases efficiency.
On board of Columbus, every angle is used – but it is used in three dimensions, for storage, instruments and consumables. Because of the zero-gravity conditions, it makes sense to arrange the instruments, work areas and storage compartments of the laboratory three-dimensionally around the astronaut. The radii recommended on Earth for optimal physiological and anatomical working areas are adhered to as far as possible in order to support smooth, fault- and fatigue-free work – but on board the space station this also applies upwards and downwards.
Terrestrial laboratories usually waste a lot of space here – especially in optimal physiological and anatomical working areas, which would be well suited for keeping instruments and materials. It can make a lot of sense to think in spheres here, too: The use of centrifuges that can be pushed under a bench (not used for bench work while sitting) frees up more work space on the bench. Especially when setting up a new laboratory, this provides an opportunity to make the arrangement as ergonomic as possible. Where are the benches located? How much bench space does each member of staff have available? Where are the storage cabinets positioned? How deep are the storage cabinets and what is kept where? Do the laboratory technicians sit at the bench or do they stand? Where are the refrigerator, centrifuge etc. located? This also includes continuous straightening-up so that everything is always in the right place, familiar to everyone.
Perfect planning in advance saves time and trouble
In order to make full use of the time available for experiments and transport capacity, all payloads, workflows and protocols are optimized down to the smallest detail before launch. To save time and eliminate potential errors, all consumables and materials required for each experiment are packed into individual storage bags and clearly labelled.
Optimal preparation of experiments in the form of test kits saves time and increases efficiency.
Mehr erfahren
Weniger lesen
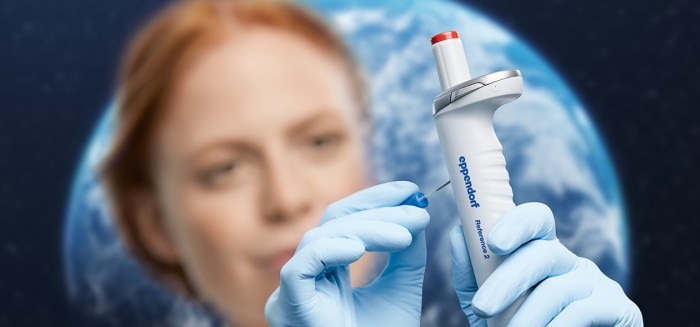
Durable equipment saving space and weight
As there is no room for back-up gear, the most important factors when selecting laboratory equipment are maximum durability and reliability, low weight and low susceptibility to malfunctions or faulty calibration. This is why in orbit, i.e., particularly reliable pipettes are used, made from extremely stable highperformance plastics such as Fortron® and PEEK.
Due to their extreme stability, durability and light weight, these materials are widely used in space vessels – and they guarantee long durability and perfect ergonomics on Earth as well. For instance, the intuitive usability prevents erroneous handling and color coding facilitates the proper operation of the systems.
When automation is key and when it is not
In space travel, there is a conflict of objectives to be resolved in the topic of laboratory automation and robotics : on the one hand it makes sense to relieve astronauts of as many routines as possible and to automate repetitive tasks that have to be performed with great precision; on the other hand, the astronauts must be able to repair any device on their own using just their knowledge, creativity and – even unconventional – means available on board. The restrictions on weight and volume prohibit carrying a back-up, as each gram must be pushed against gravity at 9 x g to reach 28,000 km/h. In addition, automatic dispensers have a number of major limitations that disqualify them for being used aboard the ISS: they are too heavy, too large and, above all, they do not usually allow liquids to be dispensed against the wall of the vial, as this would require either the plate or the dosing unit to be tilted. Furthermore, there are no high throughput requirements on the ISS.Thus, astronauts usually have to operate without pipetting robots, i.e., the profound training and extreme accuracy of all team members are of immense importance. In any case, they must use an identical pipetting technique and pipetting habits in order to prevent errors and achieve consistent, reproducible results. Switching between forward and reverse pipetting or different habits when wiping off the pipette tip could lead to serious measuring errors.
On earth, automated liquid handling guarantees the quality of results in high throughput experimenting . But: if automation is out of the question in individual cases, all employees involved must use the same pipetting techniques and standardize their pipetting habits.
A closer look at the special challenges and ways of solving issues on board a scientific laboratory in orbit can always provide us with some valuable ideas on how to optimize laboratories on Earth. As it comes to limitations of space, time and weight, we can use a lot of ideas to improve the staff’s surroundings and make workflows more efficient.
As there is no room for back-up gear, the most important factors when selecting laboratory equipment are maximum durability and reliability, low weight and low susceptibility to malfunctions or faulty calibration. This is why in orbit, i.e., particularly reliable pipettes are used, made from extremely stable highperformance plastics such as Fortron® and PEEK.
Due to their extreme stability, durability and light weight, these materials are widely used in space vessels – and they guarantee long durability and perfect ergonomics on Earth as well. For instance, the intuitive usability prevents erroneous handling and color coding facilitates the proper operation of the systems.
When automation is key and when it is not
In space travel, there is a conflict of objectives to be resolved in the topic of laboratory automation and robotics : on the one hand it makes sense to relieve astronauts of as many routines as possible and to automate repetitive tasks that have to be performed with great precision; on the other hand, the astronauts must be able to repair any device on their own using just their knowledge, creativity and – even unconventional – means available on board. The restrictions on weight and volume prohibit carrying a back-up, as each gram must be pushed against gravity at 9 x g to reach 28,000 km/h. In addition, automatic dispensers have a number of major limitations that disqualify them for being used aboard the ISS: they are too heavy, too large and, above all, they do not usually allow liquids to be dispensed against the wall of the vial, as this would require either the plate or the dosing unit to be tilted. Furthermore, there are no high throughput requirements on the ISS.Thus, astronauts usually have to operate without pipetting robots, i.e., the profound training and extreme accuracy of all team members are of immense importance. In any case, they must use an identical pipetting technique and pipetting habits in order to prevent errors and achieve consistent, reproducible results. Switching between forward and reverse pipetting or different habits when wiping off the pipette tip could lead to serious measuring errors.
On earth, automated liquid handling guarantees the quality of results in high throughput experimenting . But: if automation is out of the question in individual cases, all employees involved must use the same pipetting techniques and standardize their pipetting habits.
A closer look at the special challenges and ways of solving issues on board a scientific laboratory in orbit can always provide us with some valuable ideas on how to optimize laboratories on Earth. As it comes to limitations of space, time and weight, we can use a lot of ideas to improve the staff’s surroundings and make workflows more efficient.
Mehr erfahren
Weniger lesen
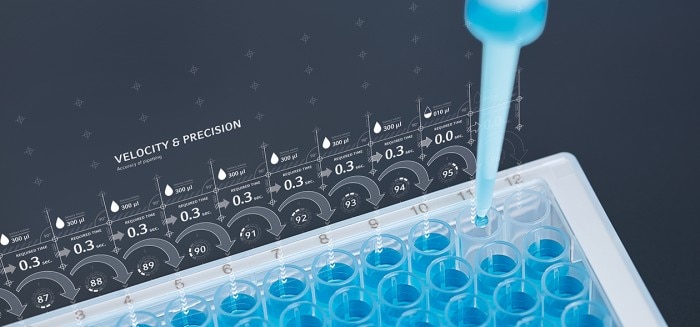
Find out more from outter space, click here.
Mehr erfahren
Weniger lesen
Mehr erfahren
Weniger lesen
Mehr erfahren
Weniger lesen