MENU
BR | BRL
BR | BRL
-
- Centrífugas de bancada
- Centrífugas de piso
- Centrífugas refrigeradas
- Microcentrífugas
- Centrífugas multiúso
- Centrífugas de alta velocidade
- Ultracentrífugas
- Concentrator
- High-Speed and Ultracentrifuge Consumables
- Tubos de centrífuga
- Placas de centrífuga
- Gerenciamento de dispositivo
- Gerenciamento de amostras e informação
-
- Pipetagem manual & dispensação
- Pipetas mecânicas
- Pipetas eletrônicas
- Pipetas multicanal
- Pipetas de deslocamento positivo e dispensadores
- Sistema automatizado de Pipetagem
- Dispensadores de bancada
- Controladores de pipeta
- Ponteiras de pipeta
- Consumíveis de automação
- Acessórios para pipetas e dispensadores
- Acessórios de automação
- Serviços para pipetas e dispensadores
Sorry, we couldn't find anything on our website containing your search term.
GMP info
Regarding suitability of Eppendorf bioprocess equipment in GMP-regulated applications, please reach out to your Eppendorf sales representative.
Monoclonal Antibody Production in Bioreactors
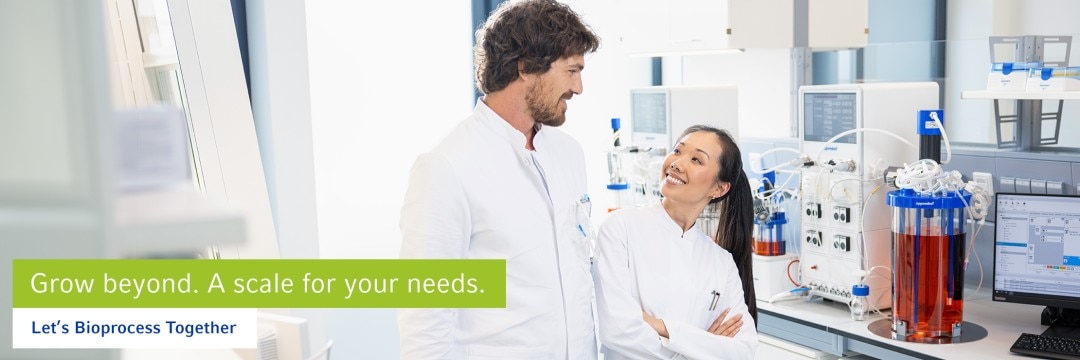
At Eppendorf, our aim is to empower your upstream bioprocessing to produce monoclonal antibodies and other therapeutic proteins in bioreactors. We provide tools that help you accelerate process development by working in parallel, increasing turn-around, and leveraging the full potential of bioprocess data. We help scaling up your process from R&D to clinical and commercial manufacturing while maintaining quality and yield. We pay attention to your specific challenges, and we work together with you to solve them. So come and talk to us, we are all ears.
Read more
Read less
We help you leverage bioprocess intelligence
Develop more reliable, more productive processes faster
We offer orchestrated bioreactor, software, and service solutions that let you combine experimental efficiency with smart use of data. Discover our bioprocess solutions that support you to increase speed through parallel processing, automation, and efficient data analysis. Find out how our software solutions can leverage the power of artificial intelligence to translate data into strategies to increase product yield and quality.
Read more
Read less
Reduce risks and save time with single-use technology
Our single-use technology helps you increase throughput, flexibility, and safety in bioprocessing. BioBLU® Single-Use Bioreactors eliminate the need for labor-intensive cleaning procedures, cleaning validation, and hold time validation. With built-in measures to minimize the risk of contamination, they enable you to act quickly while significantly reducing the risk of costly and time-consuming batch failures in both research and manufacturing environments.
Read more
Read less
Seamlessly transition from R&D to manufacturing
Maintain consistency and quality as you scale-up. Our scalable bioprocess solutions help you seamlessly translate your R&D successes into manufacturing. Our solution package of bioprocess controllers, bioreactors, bioprocess SCADA software, and services support the compliance of your bioprocesses with GMP requirements in clinical and commercial manufacturing.
Read more
Read less
Advance the use of your bioprocess data and simplify collaboration
Our software solutions help you advance the use of your bioprocess data, starting from remote process monitoring to process control and automation, to collaboration and contextualization of data across instruments, runs and sites. Find out more about how our software solutions and bioprocess systems work in harmony to provide a complete
upstream bioprocessing solution.
upstream bioprocessing solution.
Read more
Read less
Get to know the Eppendorf bioprocess products
The Eppendorf bioprocess portfolio offers scalable bioprocess systems, single-use bioreactors, software solutions, and services to efficiently develop processes and move them from R&D to manufacturing.
Read more
Read less